Occupational health and safety is a key element for every company – no matter what or where work is carried out, just like in everyday life, something can happen at work at any time. In Germany alone, around 787,000 reportable workplace accidents occurred in 2022. Occupational health and safety contributes to the well-being of employees and therefore ultimately also to the well-being of the company, because occupational health and safety includes everything that helps to enable people to work in a humane manner and therefore also includes aspects of hygiene and health protection in addition to occupational safety. Occupational health and safety therefore also serves to increase the quality of work. Because if the employees are satisfied, the customers, suppliers etc. usually are too. This means that occupational health and safety ultimately also influences the profitability of a company.
You need products for your occupational safety and hygiene – you’ll find them in the RAJA shop!What is the difference between occupational safety and health and safety at work?
The terms occupational safety and occupational health and safety are often used interchangeably, as both have a common goal: the hazard-free performance of the job!
Every employer is legally obliged to ensure that their employees can carry out their work safely. Occupational safety is just as much a part of occupational health and safety as health protection.
What is occupational health and safety?
Occupational health and safety describes the bundling of all measures and tasks in occupational health and safety. Whether in the office or in the factory – occupational health and safety is mandatory for all companies in Germany and is regulated by law in Social Code VII (SGB VII), the Occupational Health and Safety Act (ArbSchG) and the regulations of the employers’ liability insurance associations. Occupational health and safety determines the protection against work-related hazards, accidents and illnesses. The employer and the responsible managers in the company are responsible for the organisation and implementation of occupational health and safety. A distinction is made between different types of occupational health and safety:- Organisational or general occupational health and safety: this includes all regulations that safeguard the health and lives of employees and serve to prevent accidents at work or occupational illnesses.
- Social occupational health and safety: in addition to working time protection,this also includes all regulations for particularly vulnerable employees, such as maternity protection for pregnant women, youth labour protection, equal treatment, etc.
- Technical occupational health and safety: includes all measures and facilities that serve the safety of employees. This includes, for example, protection against dangerous work equipment and hazardous substances, the safety of workplaces (fire protection, regulation of first aid measures, etc.), protection against noise, vibration or radiation.
- Medical occupational health and safety: protection against work-related illnesses, occupational diseases or work-related health hazards, as well as preventive health care by specialised personnel such as company doctors and employers’ liability insurance associations .
What is occupational safety?
Occupational safety is the goal of occupational health and safety. It is understood to mean a state of hazard-free working. To achieve this, accident risks and general occupational health hazards must be minimised, if not completely eliminated. While the Occupational Health and Safety Act deals with measures and processes, such as risk assessment or the obligation to instruct employees, the Occupational Safety Act (ASiG) is, so to speak, the supervisory body for occupational health and safety. This is because the ASiG regulates the employer’s obligations, for example to appoint an occupational safety specialist and a company doctor to advise on occupational health and safety issues and ensure compliance with regulations.
What does health protection involve?
Occupational health protection is concerned with the long-term effects of work on the health of employees. The aim is to prevent work-related health problems and occupational illnesses.
How is occupational health and safety regulated? – Statutory provisions
Occupational health and safety in Germany is regulated in a dual system: on the one hand by the state itself and on the other by the statutory accident insurance institutions. The state has the task of monitoring and controlling occupational health and safety in accordance with European occupational health and safety legislation and the Occupational Health and Safety Act (ArbSchG). There are a number of things to consider:
The basic requirements are regulated by various laws. They are supplemented by ordinances, administrative regulations, decrees and implementing ordinances that regulate the practical implementation of occupational health and safety. In addition, there are the generally recognised rules of technology, hygiene and occupational medicine (VDI/VDE, BMA guidelines, DIN/DIN-EN).
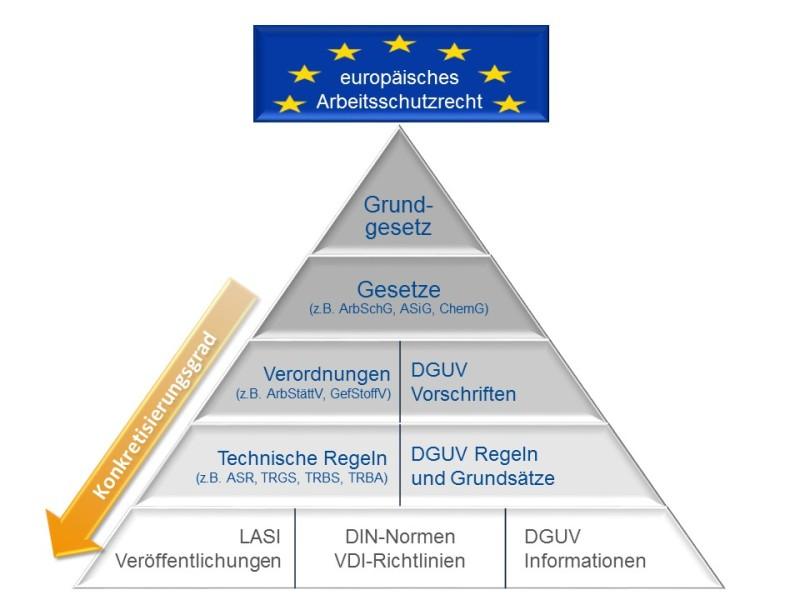
The supervisory bodies of state occupational health and safety (federal government, federal states) are the trade supervisory offices in the respective federal states. The technical supervisory services and the trade supervisory offices form a joint, state-related body. The trade supervisory authorities can exercise their right to inspect and audit a company at any time. The corresponding authorisations are regulated in § 22 ArbSchG.
The respective state authorities co-operate closely with the statutory accident insurance institutions when carrying out inspections. The statutory accident insurance institutions are the employers’ liability insurance associations (BG). Every company in Germany is a member of a trade association, depending on the economic sector or industry. They are authorised to issue and monitor accident prevention regulations. These regulations and their subsequent regulations (BG regulations) are also legally binding. All employees, including trainees and certain other groups of people, are insured against the consequences of accidents at work, commuting accidents and occupational illnesses through their company’s membership of the relevant accident insurance organisation. Employers pay the accident insurance contributions.
In accordance with the Seventh Book of the German Social Code (SGBVII), the core tasks of statutory accident insurance are
- Prevention: to prevent insured events, i.e. accidents at work and occupational illnesses, as well as work-related health hazards,
- Rehabilitation: restoring the health and performance of insured persons after the occurrence of insured events
- Compensation: To compensate insured persons or their surviving dependants by providing cash benefits
- In order to fulfil their prevention task, the accident insurance institutions issue their own binding regulations(autonomous legislation) in addition to the state laws and provide recommendations for the implementation of regulations. These DGUV regulations are also legally binding. They are often very specialised and specifically geared towards individual sectors, hazards or activities .
What are the components of occupational health and safety?
The risk assessment is to a certain extent the basis of occupational health and safety. It is a procedure for assessing the hazards and stresses to which employees are exposed as a result of their working conditions. The company management is responsible for its implementation and documentation. If working conditions are changed, the risk assessment must also be reviewed accordingly and adapted if necessary.
A risk assessment must be carried out for each workplace/activity, applying the so-called STOP principle. It is considered in turn whether and how the hazard can be minimised by:
- Substitution(e.g. by using other work processes, materials),
- Technicalsolutions (e.g. structural separation, extraction)
- Organisationalmeasures (e.g. time limits, training)
- Personalprotective measures (e.g. PPE)
can be reduced.
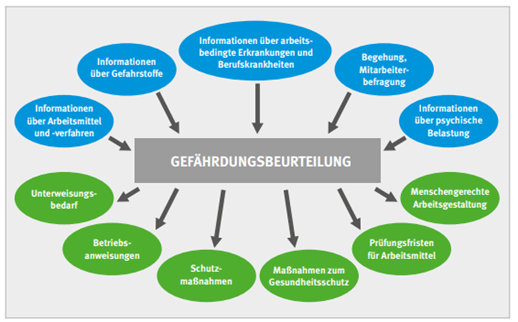
Depending on the work area, the appropriate protective measures are then derived and implemented from the risk assessment, which also includes instructing employees, creating operating instructions and much more.
Personal protective equipment – What is PPE?
If a hazard in the workplace cannot be averted by technical or organisational measures, the employer is obliged to provide his employees with personal protective equipment (PPE) free of charge and to train them accordingly.
Personal protective equipment within the meaning of the PPE Usage Ordinance (PSA-BV) is any equipment/work clothing intended to protect employees from a risk to their safety and health, as well as any additional equipment used for the same purpose and associated with the personal protective equipment.
PPE therefore includes all parts of protective work clothing: safety helmets, e.g. construction site helmets, safety goggles, protective shields, hearing protection, respiratory masks, safety shoes, protective gloves, chemical protective clothing, safety harnesses, life jackets, stab protection clothing, but also special skin protection products.
PPE may only be made available on the market if it complies with the provisions of the European PPE Regulation (“Regulation (EU) 2016/425 of the European Parliament and of the Council of 9 March 2016 on personal protective equipment and repealing Directive 89/686/EEC”).
Is hygiene part of occupational safety?
Quite clearly: Yes – general hygiene requirements are also derived from the employer’s duty of care (ArbSchG and DGUV 1). This is concretised in the Workplace Ordinance, for example for break rooms or sanitary facilities, and the cleaning of workplaces is also regulated in the Workplace Ordinance. The risk assessment is also decisive here, as there are of course different hygiene and cleaning requirements depending on the type of business or industry.
There are very specific hygiene requirements for companies that deal with biological agents, for example waste disposal companies, laboratories, building cleaners or the healthcare sector, to name but a few. Here there are specific requirements regarding work clothing, hand hygiene, cleaning of work areas and occupational health precautions. Companies that work with food must also fulfil special hygiene requirements, such as the HACCP concept, which is primarily aimed at food safety, but also covers the protection of employees.
Is ergonomics part of occupational health and safety?
As already mentioned, prevention is a decisive factor in occupational health and safety. For example, every employer is obliged to provide their employees with an ergonomic workplace. When designing workplaces ergonomically, various parameters must be taken into account, such as climatic conditions, workplace temperature or humidity, but also issues such as noise and lighting, as well as the correct working posture to prevent musculoskeletal disorders.
This also means that aspects relating to occupational health and safety must be taken into account at the planning stage when designing workstations. DGUV Rule 108-007 applies to storage facilities and equipment and serves as an aid for employers when implementing occupational health and safety regulations or accident prevention regulations and helps to prevent accidents at work and occupational illnesses. The DGUV Rule can be seen as a guideline for the implementation of safety measures and shows technical solutions. These include the correct planning and labelling of internal traffic routes, as well as the safety marking and testing of work equipment, for example shelving.
Conclusion – What does the future hold for occupational health and safety?
Occupational health and safety is an indispensable part of the world of work that is not just about fulfilling legal regulations and standards, but rather about creating a safe, healthy and productive working environment that supports the physical, mental and social well-being of employees.
Effective occupational health and safety reduces the number of accidents at work, work-related illnesses and ultimately downtime, which not only minimises human costs but also the financial burden on companies. It also promotes a positive work culture in which employees feel valued and safe, which in turn can increase motivation and therefore productivity.
Occupational health and safety is always a shared responsibility: the employer is legally obliged to take the necessary health and safety measures and provide a safe working environment, but the employee is equally responsible for observing and complying with these measures.
Occupational safety is not a rigid construct – in a time of rapid technological change and the increasing digitalisation of the world of work, occupational safety measures must be constantly adapted and further developed to meet new risks and challenges. The COVID pandemic has recently shown that occupational health and safety standards need to be constantly scrutinised, revised and adapted. Increasingly mobile work, which is no longer tied to a fixed place of work, presents employers in particular with challenges in terms of occupational health and safety law. Due to the increasing digitalisation of the world of work, the mental health and safety of employees is also increasingly becoming the focus of occupational health and safety – since 2013, mental stress has been explicitly included in Section 5 (6) of the Occupational Health and Safety Act.
In an increasingly complex working environment, occupational health and safety should not only be seen as a duty, but also as an investment in the future of a company and the well-being of its employees. A proactive approach in this area not only protects individuals, but also strengthens the competitiveness and sustainability of companies and organisations.