E-commerce is changing the Belgian online landscape at breakneck speed. Eurostat figures showed that 21% of Belgian companies already had a webshop in 2017. Online consumption is also on the rise. According to BeCommerce, 86.5 million online purchases were made last year. This does not even include the B2B market! So how do you get your products from the manufacturer to the end customer quickly? Here, efficient warehouse management plays a key role. With these 10 tips, we show you how we have made our warehouse hyper-efficient over the years. It allows us to ship many hundreds of large orders daily to seven European countries – all within 24 hours.
► 1. Choose a strategy according to the number of daily shipments
The first lesson is probably no surprise: the size of your business determines your strategy. First of all, be aware of how many orders need to be processed daily. Only then choose one of the logistics strategies below.
Number of orders/day | Which strategy is appropriate? | How do you proceed? |
≤ 50 | With a warehouse of up to 500 m² and a team of only 5 people, no specific strategy is needed. | Each picking is carried out separately. Each team member takes on several tasks. |
≥ 50 | Work out a fixed structure. | Pickings are grouped and each team member will perform 1 specific task. |
≤ 1000 | In addition to a fixed structure, choose automation. | WMS or other management software will take over certain tasks from staff. Packing machines help you save time and costs. |
≥ 1000 | Outsource (part of) the work to third parties. | An external company takes over the work at times when the number of orders peaks. |
► 2. Optimise the working environment
- Limit the number of moves: locate and identify your products easily and quickly with, for example, warehouse labels. If you set this up clearly and logically, you will complete each picking route smoothly.
- Move heavy orders efficiently: equip your warehouse with conveyors, forklifts and transpallets, avoiding a lot of physical discomfort for your employees.
- Invest in high-quality equipment such as barcode scanners, computer screens and a smart warehouse management system (WMS). A WMS remembers where the right products are, preventing errors throughout the process. See how we used a powerful and intelligent WMS ourselves in this video:
► 3. Demarcate your warehouse into zones
If you don’t use your warehouse space correctly, the disorder will soon become too much for you. Therefore, apply the following tips:
- Make sure all products are numbered and create fixed paths that easily lead employees to the right product.
- Demarcate your warehouse visually. Create a buffer stock zone, storage areas, arrival and dispatch zones and transport zones. For this, use signage tape, for example, that you can stick on the walls or floor.
► 4. Automate your packaging process
If you pack more than 15 orders a day, then it is worth bringing in a packing machine. Machines help you produce padding material very quickly and close your parcels easily. Don’t know which machines exist? No problem! Download our guide to packaging machines and systems here and become a real expert yourself.
► 5. Create an inventory for your bestsellers
Every company has certain products that always fly out the door quickly. These ensure high sales and are therefore very important. Therefore, create a stock room especially for these products. Preferably provide this space close to the packing and shipping area and save a lot of time.
► 6. Process your products according to their logistical properties
Improve your warehouse management by organising your goods according to their properties:
- Heavy or bulky products: these require special management that probably involves transport machines. So make sure there is sufficient movement space around the storage areas for this.
- Fresh products: these are best stored all together in a refrigerated area.
- Personalised products: provide a separate area for this because these products are probably no longer stored in your warehouse. They should go directly from the transit area to the packing station and thus to your customer.
► 7. Do cross docking
With cross docking, goods you receive are no longer stored in a warehouse but immediately prepared for shipment. This saves a lot of storage space and says goodbye to deadlines and time-consuming movements. This technique is useful for personalised products that you receive directly from the manufacturer.
► 8. Process similar products at the same time
With this, you save significantly on your picking time. If your logistics system registers multiple items of the same product, you can pick them at the same time – even if they are orders from different customers. This way, you can easily avoid unnecessary movements.
► 9. Trace stock shortages in good time
Managing inventory shortages remains a headache for many logistics managers. These shortages disrupt the production chain and lead irrevocably to customer dissatisfaction. Therefore, together with customer service and sales teams, start an automated procedure. This usually involves an automatic e-mail alert when a particular product is back in stock.
► 10. Carry out regular quality checks on
Erroneous orders are not appreciated by customers. It is a big challenge to avoid these mistakes as much as possible. It is therefore best to check an order on arrival, picking, packing and shipping. Perform this check with a barcode scanner so you immediately know whether the product was linked to the right customer or order. You will quickly see that the number of mistakes drops dramatically.
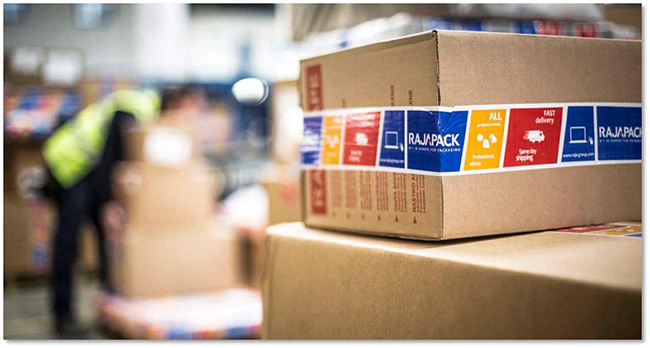
- Organisation is key. Structured warehouse management is key in any logistics centre. Best also use packaging machines to keep everything running smoothly.
- A pleasant and safe working environment protects your employees' health and improves productivity.
- Moreover, do not forget to choose a good courier. He will be able to easily track your parcels to their destination