Managing a warehouse is not a simple job. Logistics is key for all companies, so it is useful to know the performance indicators, or KPIs, that are involved in order management tasks in order to streamline and optimise all the processes developed within a warehouse.
What are KPIs?
KPIs, or Key Performance Indicators, are key performance indicators that help identify areas of improvement to optimise any business. In order to know precisely how the warehouse supply chain is performing, it is important to measure. KPIs provide valuable information about what is happening in the company and help to make the right decisions for the future.
The 5 must-have KPIs for order management
Although there are many KPIs that can be monitored, these are the five that we consider essential when evaluating order management in the warehouse.
1. Order delivery time
The delivery time of an order takes into account the period from the customer’s request to the receipt of the product. This KPI is key to measuring customer satisfaction, as the lower the delivery time, the higher the customer satisfaction.
In order for everything to go smoothly and for the order to arrive on time, there can be no mistakes in the order of the following chain of tasks:
- Receipt of the order
- Picking and packing
- Dispatch of the order
A multi-purpose trolley will help in the early stages of order preparation when products have to be located in the warehouse.
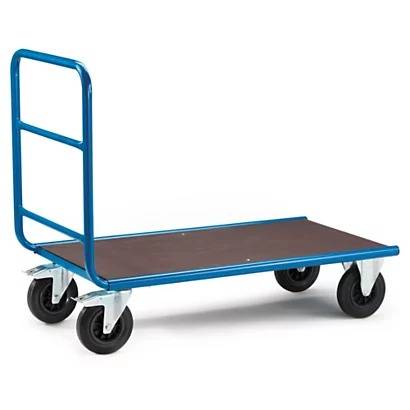
2. Internal order cycle time
This is the time it takes to complete an order from the arrival of the order to the departure of the package from the warehouse, so logistical flows must be taken into account. The formula would be as follows:
Cardboard boxes are presented as a safe, quality and EcoResponsible option for the transport of all types of goods.
Internal order cycle time = Date of order entry – Date of dispatch
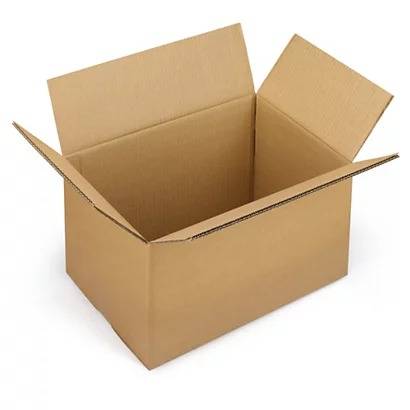
3. Orders dispatched per hour
This KPI influences the cost of order preparation. It is an essential indicator that affects the efficiency of the process and reflects the productivity of the operators. It measures the number of orders that are ready to be dispatched on an hourly basis.
Close attention should be paid to the prevention of musculoskeletal disorders, as this can slow down the process. Improvements such as automation in intralogistics help to speed up the pace; for example, a crate sealing machine is very practical in terms of saving time when sealing packages.
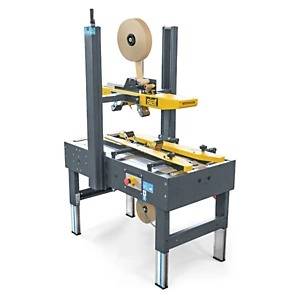
4. Perfect order rate
As the name suggests, this KPI measures the number of shipments that have been delivered perfectly, i.e. without any incidents in the fulfilment of these stages:
- Correct product selection
- Shipment within the estimated timeframe
- Reception in perfect condition
The main thing is that a package is delivered without any setbacks, but as orders go through different stages from the time of purchase to arrival, sometimes this is not 100% achieved. To calculate the perfect order rate, the following formula has to be applied:
Perfect order rate = Orders completed without incident / Total orders placed.
To ensure that an order reaches the customer perfectly, it is essential that the package is properly identified. Stickers allow the buyer’s details to be recorded in detail so that there is no confusion on receipt.
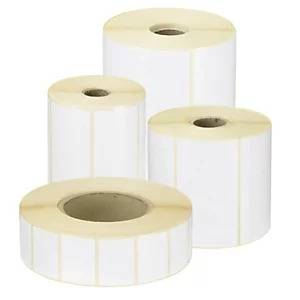
5. On-time delivery rate of orders
This KPI reflects the percentage of shipments that have been delivered within the deadline agreed with the customer. This would be the formula for its calculation:
On-time delivery rate = Deliveries made within the agreed timeframe / Total deliveries made.
Variable-height cardboard boxes are a very practical solution for maintaining punctuality during the peak season, e.g. the so-called holiday season, which includes Black Friday and Christmas and generates a logistical peak for a wide variety of businesses. With a single packaging reference, orders of different volumes are covered, and operators don’t waste a second calculating the optimal packaging size for each request.
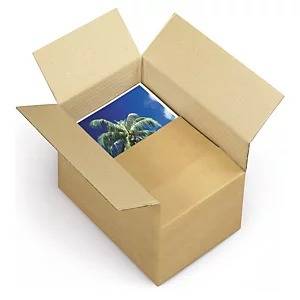
As you can see, these 5 KPIs are indispensable for monitoring order management in the warehouse. At RAJA® we understand the importance of maximising throughput, which is why we want to offer you the best quality products to ensure your shipments are optimal. Check out our warehouse equipment section!