The time spent preparing orders in warehouses is a key element in the calculation of the overall logistics cost, and all companies seek to optimise it: this is why you should carefully choose your preparation method according to your shipping thresholds and your activity.
The order picking process consists of organising the highlights of a package in the warehouse:
- Picking: the operator picks the items needed to create the orders.
- Sorting: once the items have been selected, they are divided into orders.
- Packing: the items are packed once they have been grouped together.
By the end of this article, you will have discovered 3 order picking methodologies to improve your transport and logistics strategy while eliminating errors in your deliveries.
What is order picking?
When the warehouse receives large quantities of goods, they must first be stored on the shelves and then deliver the products ordered on a daily basis to a “picking” area.
This area allows you to store
- Products in small quantities
- Best sellers.
- Products accessible by hand.
It is in this step that products are searched for on the warehouse shelves, then transported to the packing area and then to the shipping area.
Picking, like the rest of your warehouse, can be optimised through different methods.
Note: In a shop, this picking process is called “purchasing”. Note, however, that this article is dedicated to picking methods in the supply chain of a warehouse. |
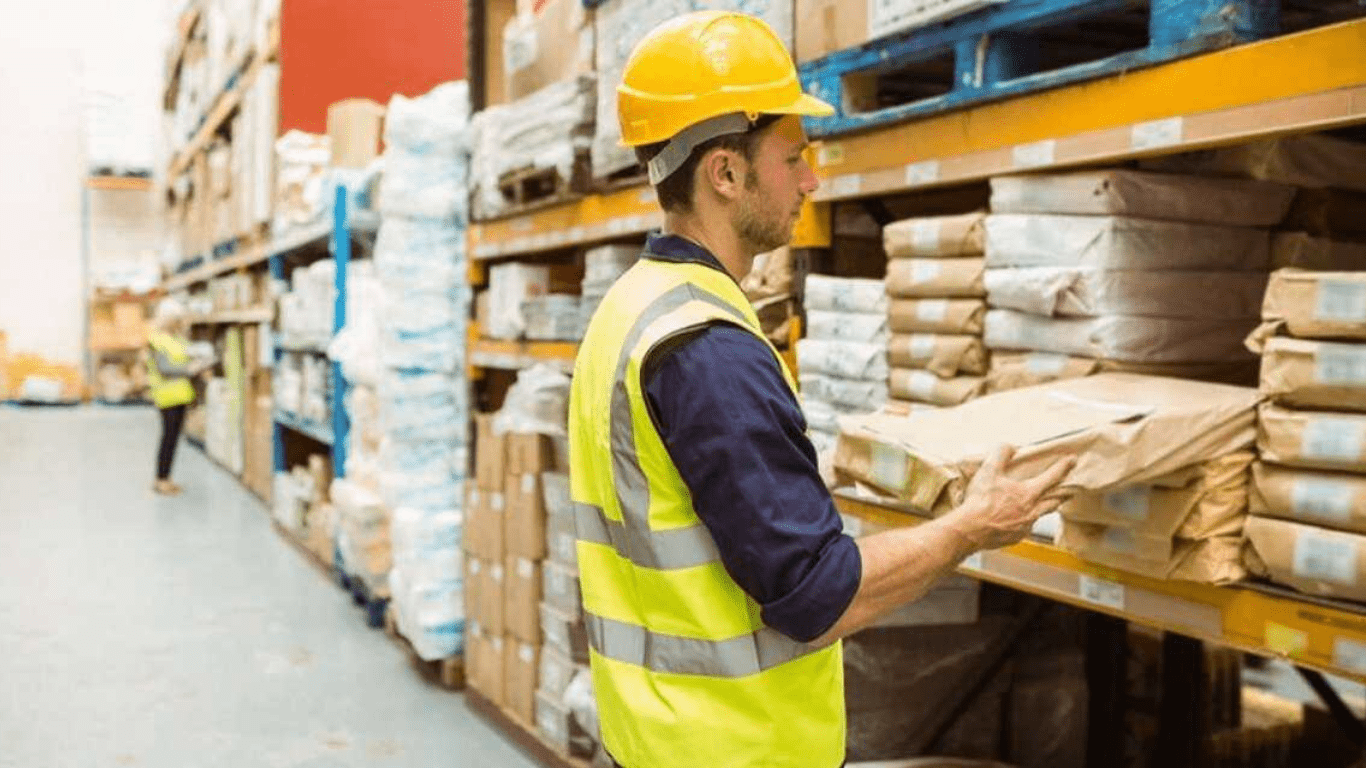
The “Pick and Pack” method
How does the “Pick and Pack” order picking method work?
- The order picker picks the required goods indicated on his order form, takes them to the packing area and then picks the products again for another order. This method is obviously not the fastest, but it is the most suitable for very low same-day shipping thresholds, e.g. for small e-commerce activities.
- Pick and pack” is the best method: when the order picker picks all items from several orders at the same time to distribute them in an order picking trolley, before packing them.
The “Put to light” method
How does the “Put to light” method work?
Literally meaning ‘put to light’, this method works with trolleys equipped with illuminated displays to show the operator where to pick and drop off the required products.
This allows efficient bulk picking from bulk stock.
The operator then drives with his trolley to the place where the orders are distributed: his ‘Put to light’ displays will light up in front of each location to show him which bin or box to put his item in.
This method has two main advantages:
- This guidance system allows the logistics operator to prepare and consolidate several orders at once.
- It allows the order picker to minimise the risk of errors or omissions, thanks to optimal traceability of his order picking activity.
The “Pick by light” or global collection method
This picking method also works with light signals and is very useful when the order threshold is high, to minimise the risk of errors.
LEDs and luminous messages are legibly displayed at the storage location. The operator then easily recognises the picking location of each product as well as the quantity of items to be picked.
Once the products have been picked, the operator triggers the validation of his sales order, received directly by the central inventory management terminal.
This allows continuous replenishment from the storage area to the picking area, thus avoiding interruptions in the process.
The operator then scans each item for handling and places it in the location indicated by a light indicator in the aisles.
The orders are then picked and taken to the packing area. Thanks to the light signals, the operator knows at a glance the current status of the orders to be prepared, without having to consult the order forms:
- Green = complete
- Red = incomplete.
This method also has many advantages:
- It allows you to prepare many orders at the same time.
- It increases the productivity of the entire order preparation supply chain.
- It reduces the risk of forgetfulness or picking errors thanks to an effective light signal.
- It works in harmony with the warehouse’s central inventory management system (WMS or ERP), thus reducing the time your employees have to manage inventory orders.
As a result, your productivity increases.
However, “Put to light” and “Pick by light” systems require efficient computerisation of the warehouse and generate rather high equipment costs.
Despite this, your logistics warehouse quickly gains in productivity: the number of errors in order picking is significantly reduced, logistics operators can pick more orders at once and the management system is streamlined to avoid any stock shortages.
To go further: Do you know Voice Picking, or voice command picking? This method of order picking can be very effective, but it changes the order picker’s job in the long run. |
Conclusion: what to remember about these order picking methods
- Pick and pack is a traditional method that may be suitable for logistics warehouses that do not experience a high rate of daily orders.
- To avoid human errors in order picking, such as forgetting or mixing products, automation and the “Put to light” and “Pick by light” systems are particularly recommended.
- The light indicator system excels in simplifying product and location recognition. However, this requires a certain level of equipment from your warehouse. But productivity and customer satisfaction are multiplied.