Reducing empties and fitting the packaging properly to the product is a major challenge for all businesses selling and shipping their items. Although empties cannot be touched, they represent a significant burden on the transport budget: no doubt this has already not escaped the attention of companies when analysing current packaging processes.
How can packaging be optimised to reduce transport costs, without compromising the customer’s delivery experience?
Packaging and logistics specialists, have several ways to do this. Which ones? About this in the five, following examples.
Checking the actual ’emptiness’ of packages
In order to implement any optimisation, an audit will be necessary.
It is a good idea to start reducing empties by drawing up a list of the most frequent orders, highlighting their main characteristics, such as weight, size or product type. An ERP system or an order management tool, if your company has one, will be helpful in gathering this information.
Based on a list of the most frequent orders, it will be possible to create a typology of packaging that needs to be optimised. Among these, a distinction is usually made between packaging that is
- empty more than X%,
- cardboard, too large for certain types of products,
- where fillings are most commonly used.
Creating such a document will make it possible to identify the types of packaging that most affect the transport budget in relation to the turnover they bring.
The packaging typology will be able to be optimised and, consequently, a quick return on investment.
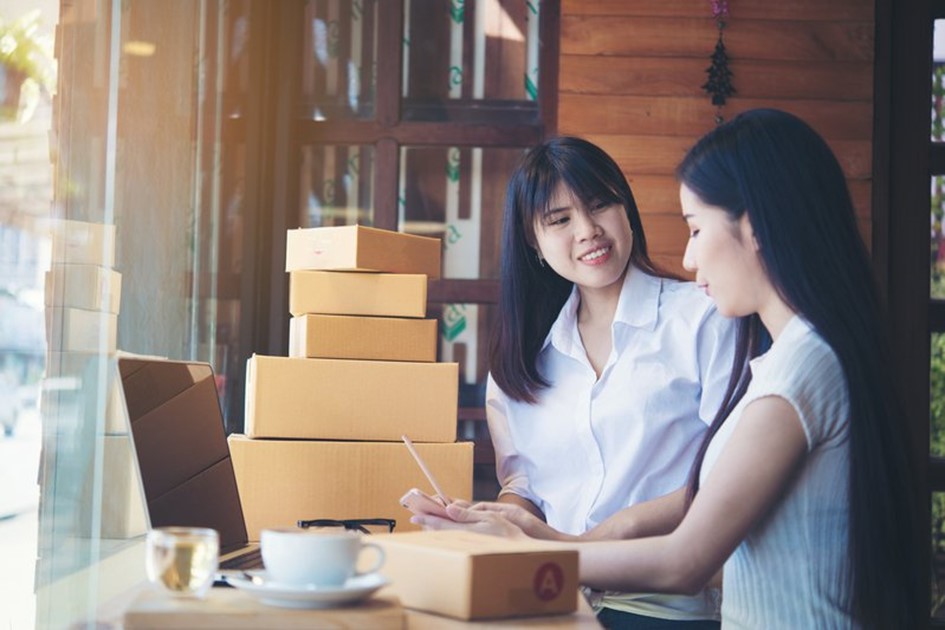
Finding the packaging adapted to the products on offer
With a list of the most frequent orders, it is possible to select the packaging that is most similar to the volume of products to be contained in it. Pay particular attention to the supplier labels placed on the packaging, which will be helpful in selecting a box for an order of a particular size.
Pay particular attention to supplier labels on packaging to assist in the selection of a box for an order of a particular size, then the reduction of voids will be more effective.
On the RAJA website, you can use one of the two search engines to facilitate your search for the ideal packaging:
When doing so, it is worth considering whether the size of the packaging used so far is appropriate.
It is usually possible to find a box size that better suits the product, thus reducing the overall volume of the order and thus minimising transport costs.
It will be a good idea to check whether it is possible to send orders of the smallest size in bubble envelopes, which take up less space than cardboard envelopes. Consequently, the reduction of empty space in this case is quick to achieve.
Undoubtedly, the most advantageous solution is customised packaging. Although their cost is usually higher than that of standard boxes, they make it possible to reduce emptiness and therefore transport costs.
3 Carry out an analysis of packaging in the various departments of the company.
Changing the way in which orders are packed, in order to reduce logistics and transport costs, is the main preoccupation of the company’s logistics and transport department.
It should not be forgotten that an analysis of packaging volumes, can have a potential impact on other areas of the company. The production department will be interested in how packaging circulates properly in the production line and how it is handled by operators. The marketing department will pay attention to the appearance of the packaging and the customer experience when unpacking the products.
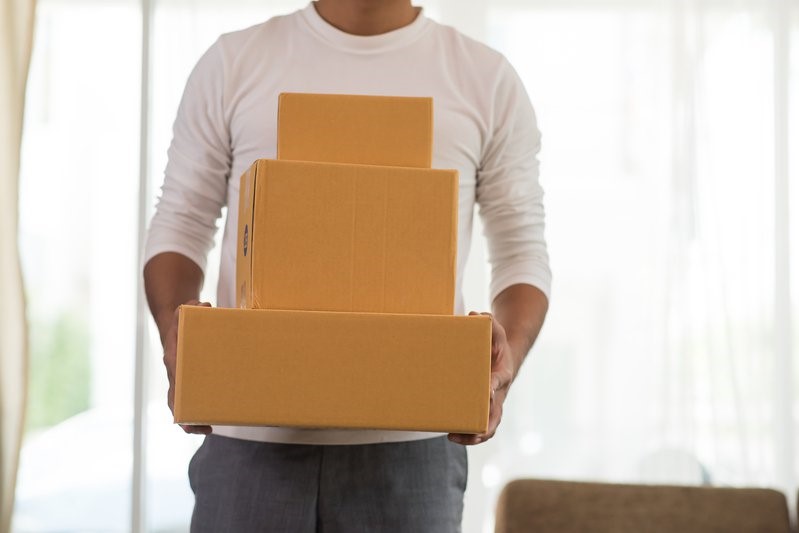
This is worth bearing in mind when optimising packaging sizes. The ideal scheme for this process, is as follows:
Ease, safety and speed of packaging (production)
+ Maintaining or enhancing a positive customer experience (marketing and customer service)
+ Maximum reduction of packaging volume and weight (logistics and transport)
= Fully optimised packaging
4 Testing and learning
Once you have decided on the changes to be implemented to optimise packaging size, it is time to implement them. In the beginning, it is advisable to apply the changes to only a small percentage of orders.
This will make it possible to test the effectiveness of a particular solution without having to revolutionise the company. At the same time, it will reduce the risk of a negative customer experience should the new packaging not meet with their approval.
During the gradual introduction of changes, two key criteria should be taken into account:
- thedurability of the packaging (whether it was delivered without damage),
- customer experience (whether the customer was satisfied when unpacking the product).
These two criteria will determine whether the optimisation is doing its job and is in line with the equation in the section above.
5 Selecting a supplier that responds quickly to the customer’s needs
It can sometimes be the case that multiple approaches are required to carry out packaging optimisation, whether because customers are not satisfied enough or the desired box size is not achieved.
In such a situation, it is a good idea to find a packaging supplier that responds quickly to customer needs. This is necessary in order to continue optimising the entire process.
By putting the above five points into practice, you will be able to reduce the volume of packaging and thus reduce transport costs.
If you need help with packaging, please contact us via tel: 801 55 3000* or e-mail: poczta@rajapack.pl. Our specialists will help you choose the best packaging solutions to suit your business.
*Costaccording to operator tariff.
Source of featured image: unsplash.com/pixabay.com