Preparing orders in a logistics warehouse can be a real challenge. One of the key stages during this type of task, which is certainly familiar to all e-commerce entrepreneurs, is picking, which has an impact on the packaging process.
From this article, you will learn what picking is, how to choose the best method for you and the specifics of picking in a warehouse, in the case of e-commerce.
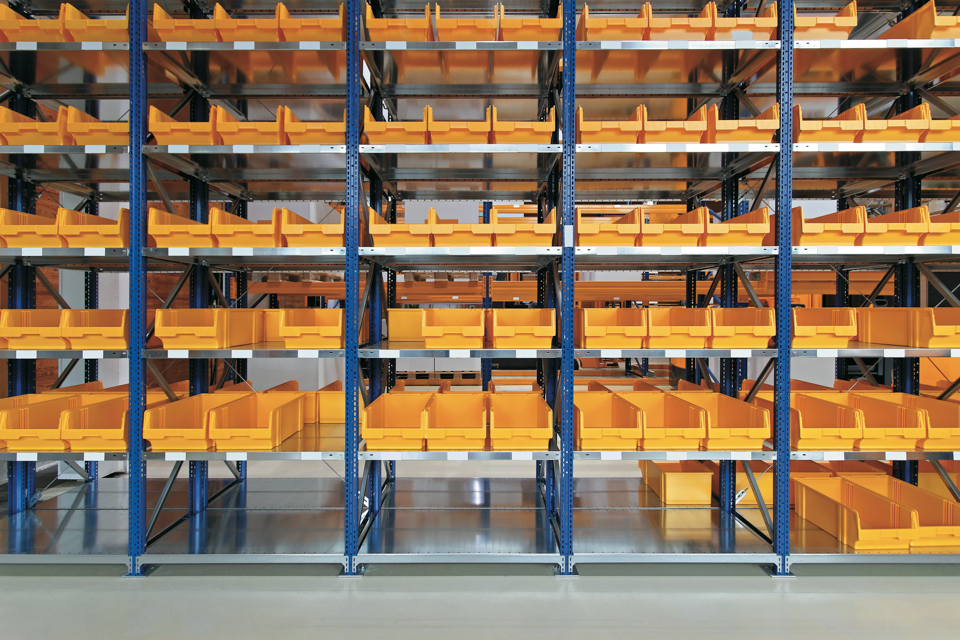
CONTENTS:
- What is picking?
- What is the difference between warehouse picking and point-of-sale picking?
- Picking methods
- How do large warehouses manage picking?
- How do you adapt your picking method when you are just starting to do e-commerce?
1 What is picking?
In English, picking is known as ‘picking’, which literally means ‘picking’. It is one of the key stages of order preparation in logistics.
In other words, it is the process whereby the items listed in the order are collected in one place so that they can be efficiently packed and prepared for dispatch.
Picking , like the other stages of goods preparation in logistics procedures, can also be optimised . The aim of this process is to place the articles needed by the operator close to the packing area. In this way, the employee’s movement around the warehouse can be reduced as much as possible, resulting in shorter order preparation times and improved handling.
2 What is the difference between picking in the warehouse and picking at the point of sale?
Two picking methods will be discussed below – the one that is used in the warehouse and the one that is used at the point of sale. This distinction is important because the optimisation of both of these methods will also take place in a slightly different way. To begin with, it is worth clarifying both concepts.
In-store picking involves preparing orders in the logistics warehouse, regardless of the method of distribution (B2B or B2C). The next step is to send the orders to the delivery location.
Pickingat the point of sale involves preparing orders in the shop. Operators take items off the shelves or bring them from the point-of-sale warehouse for subsequent delivery to the recipient’s home, or offer a ‘click and collect’ service where customers pick up the ordered products in shop.
The difference between the two types of picking is therefore analogous:
- Firstly, in-store picking is mainly for online shops that do not have a point of sale where they can store their items.
- Secondly, the in-store picking stage is followed by delivery by a carrier, so proper packaging of the shipment for transport is extremely important to prevent possible damage. In the case of picking at the point of sale, it is different, as it is the shop that directly delivers the goods to the customer, which makes the packing process much more efficient.
It is also worth mentioning that the storage of items in the warehouse differs from their storage in the shop. In the former case, it varies depending on logistical challenges, such as the seasonality of the products or the number of items the operators have to complete.
Below, we outline the picking methods that can be used.
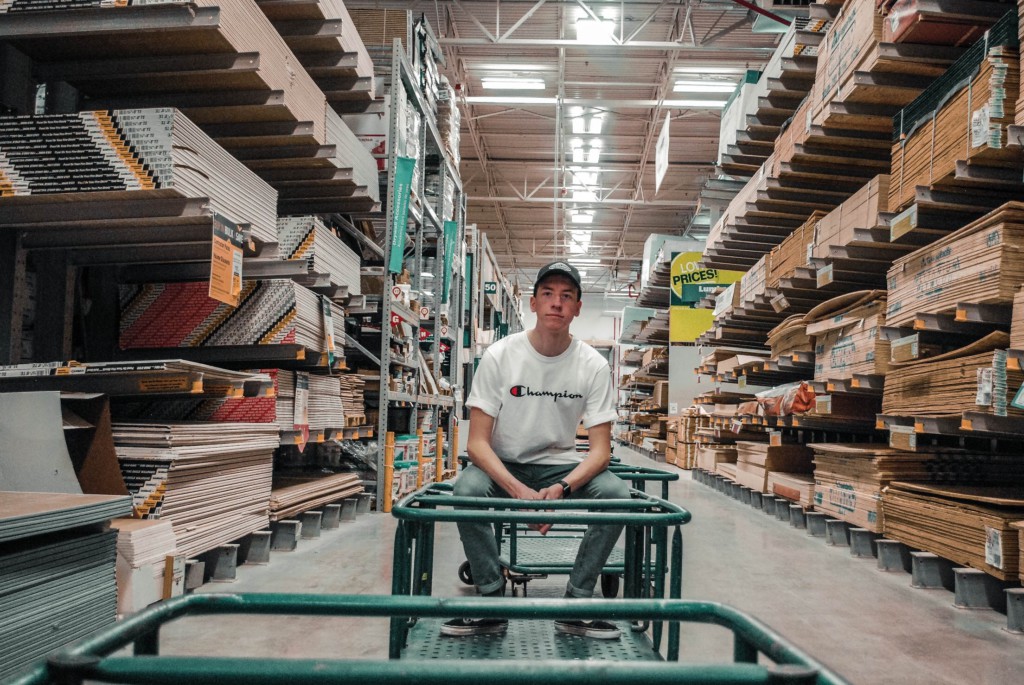
3 What are the picking methods?
Picking in the warehouse is carried out in two main systems:
- The “man to goods” process – The person preparing the orders moves around the warehouse to pick the products;
- The “goods to man” process – this is automated picking, where, using appropriate equipment, the goods move towards the operator, thus reducing the need for a worker to move around the warehouse.
Depending on the process to be implemented, different picking methods can be used.
Man-to-person picking – different methods
When moving around the warehouse, the operator can complete the goods needed for an order in several ways.
- ‘Pick and Pack’ method – the operator picks the products for one or more orders and transports them to the packing area. He or she often uses a printed order list.
- The ‘Put to Light’ method allows operators to use trolleys equipped with illuminated screens that indicate where the products needed to prepare the order are located and where they need to be taken.
- The‘Pick by Light’ method uses illuminated screens and lights that light up at that point in the warehouse where the items needed to be completed are located. The operator is easily able to find where to pick each item and read the quantity to be picked.
Each of these methods requires different equipment, which is more or less expensive.
Goods-to-man picking – automated warehouse
New technologies are continually revolutionising the functioning of logistics warehouses. Automated picking is precisely the result of their use: operators are assisted by voice-controlled IT systems, as a result of which the shipment is prepared in a mechanised manner.
Goods-to-human picking can take place in two different ways:
- robots transport the products to the preparation area,
- a central conveyor belt transports the products ready for packing to the designated areas, as in industrial production lines.
4 How do large warehouses manage picking?
The answer to this question will certainly bring the issue of optimising picking closer. Large webshop warehouses introduce storage systems that are optimised for picking.
This requires the introduction of the following elements:
- dynamic shelving and racking, adapted to the picking method chosen,
- electronic terminals that make it possible to locate where the goods are to be picked and where they will be packed;
- tools to assist in the transport of goods, such as trolleys.
Some large warehouses, (for example Amazon Prime), operate solely on the basis of an IT system. In this case, only the data determines which way the operator should move during the picking of the goods to be included in the order.
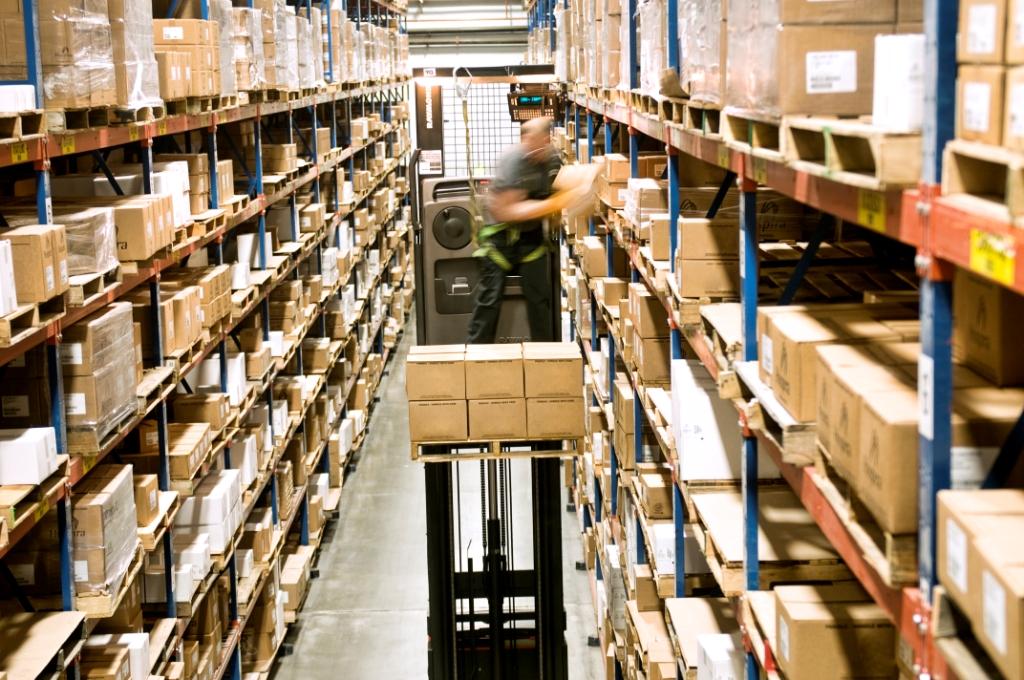
5. How do I adapt my picking method when I am just starting out in e-commerce?
Those who are just starting out in e-commerce logistics and who handle a small number of orders per day and have a small team, have no need to develop an elaborate picking strategy.
- Individual orders can be picked one at a time, and each team member’s role does not have to be limited to one activity – they can each handle picking, stocking and packing at the same time.
- Nevertheless, it is worth considering how to improve warehouse management – including how to optimise workflow and what to do to reduce the time spent on order preparation.
Product storage should therefore be determined by the following factors:
- The location of the products and how often they are ordered by customers. In this case, you can use the basic storage method – ABC. However, if you are shipping goods with a short shelf life, then you need to use the FIFO method regardless of the number of goods shipped.
- Product weights. The heaviest ones, picked first by operators, should be on the lower shelves, while the lighter ones should be higher up.
Better optimisation of picking and storage has a significant impact on the professional operation of the warehouse, which is thus better prepared to receive a large number of articles and orders.
One element of optimisation is the design of the picking table through which all shipments will pass.