The right strategy, the right procedures and work planning are extremely important in the logistics process. We give 10 tips on how to manage your warehouse effectively.
1. adapt your logistics strategy to your needs
Warehouses can vary considerably in terms of the number of orders and staff, as well as space. These factors are key to choosing the right logistics strategy to determine how to manage the warehouse.
- For up to 50 orders per day, a team of up to five people and a warehouse area of up to 500 m², each order can be picked separately and the staff can perform different functions.
- Above 50 orders, picking should be carried out for a series of orders, with team members performing specific functions. Accurate addressing of products is also required.
- When the number of orders exceeds 1,000 per day, the warehouse should be automated and an electronic warehouse management system that optimises order processing (WMS, Warehouse Management System) will be useful.
- With activity increasing periodically, logistics outsourcing can be a practical but costly solution.
2. perform quality control to minimise order errors
Proper quality control at every important stage of the logistics process (receipt of products, picking, packing, shipping) is the answer to the question of how to manage the warehouse to reduce order errors.
It will be particularly effective to control with a scanner that will verify the number and conformity of products at the time of packing.
3. structure the space in the warehouse
The larger the scale of the warehouse operations, the greater the importance of making good use of the available space.
Addressing (numbering) the products, planning the logistical paths that will lead most quickly to the product, as well as separating the different zones in the warehouse (storage, work, overstock, warehousing, order preparation, delivery reception, dispatching, etc.) can be useful.
4 Organize products according to logistical classes.
Arranging goods according to their characteristics will reduce the time of the various logistical processes and consequently improve warehouse management. For example, products can be divided into:
- Fresh.
- Heavy or awkward (requiring special equipment).
- To be customised (moving from the storage area to the production and then to the packaging area).
5. improve the working environment by investing in equipment
Improving the working environment is not only about optimising space and logistics picking paths, but also about equipping the warehouse with high-quality equipment and modern technology.
Examples include conveyor belts, lifts, pallet trucks, efficient WMS, screens or barcode readers.
6 Increase staff specialisation
In a large, professionally managed warehouse, employees are assigned to different zones: order preparation and picking, packing, addressing and dispatching, etc. The more precisely the tasks of the team members are defined, the better they know them and, consequently, the faster they perform them.
7. use the cross-docking technique
In some situations – for example, in the case of pending orders – the cross-docking technique will be useful in warehouse management.
This involves transferring goods directly from the receiving area to the dispatch area, without putting them into the warehouse. In this way, it is possible to reduce order processing times and product movements.
8. create a high turnover product zone
An analysis of the order structure gives important information on how to manage the warehouse. High-rotation products, i.e. those most frequently ordered by customers and picked by employees, should be placed in a special zone, which should be well located near the delivery, packing and shipping areas.
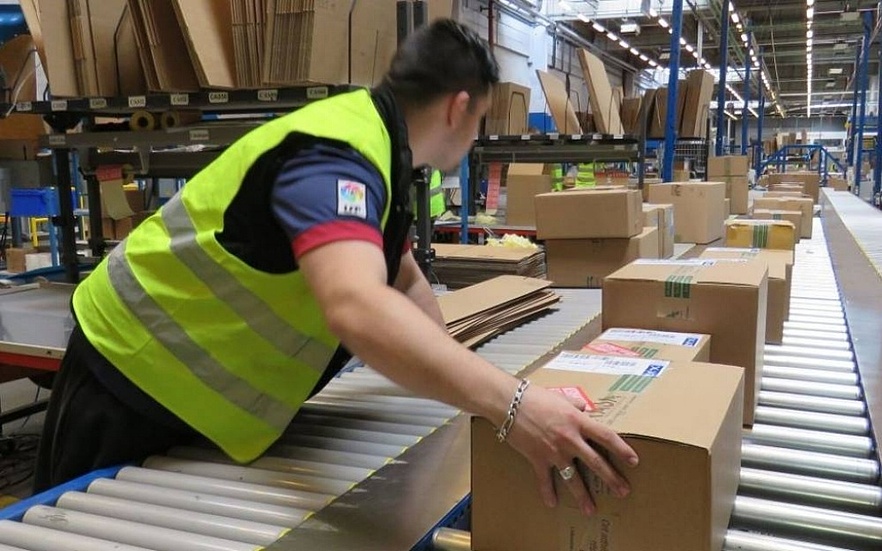
9. simultaneous preparation of orders with the same products
An ongoing analysis of incoming orders can also improve warehouse management and work planning.
For example, if some orders have the same product repeatedly, preparing them at the same time will reduce picking times, as the employee will be able to go straight away to pick more units of a given product.
10. automate the management of stock shortages
The management of stock shortages should minimise both perturbations in the supply chain and customer dissatisfaction. To this end, it is worth using standardised procedures in cooperation with after-sales service and sales teams.
The most popular method is the automatic sending of emails informing customers that stocks of a particular product will be replenished soon.
If you need help with packaging selection, please contact us via tel: 801 55 3000* or e-mail: poczta@rajapack.pl.
Our specialists will help you choose the best packaging solutions to suit your business.
*Costaccording to operator tariff.