Many companies underestimate the importance of professional filling and padding. Those who cut corners here pay for it later: through returns, damaged goods, dissatisfied customers and loss of image. Filling and padding: In this article, you will learn why they are not the same thing (and why both are necessary!), which physical principles are at work, which materials you should use and when, and how you can save costs without losing protection.
The economic importance of filling and padding material
According to the German Parcel and Express Logistics Association (BIEK), over 4.15 billion B2C and B2B shipments were transported in Germany in 2023. Around 25-40% of packaging costs are attributable to filling and padding material, depending on the industry. With the right materials and the right technology, there is therefore a lot of potential for optimisation and savings. However, there is one thing you should not do: Do without padding or filling! This is because a lack of padding (or incorrect padding) causes billions in damage every year – especially to electronics, glassware and machine components.
Definition: Filling vs. padding
Even though the terms are often used interchangeably, they have different functions in packaging physics:
- Filling = preventing movement
- Cushioning = dissipate impact energy
⚠️❗ ⚠️❗ ⚠️❗ ⚠️❗ ⚠️❗ ⚠️❗ ⚠️❗ ⚠️❗ ⚠️❗ ⚠️❗ ⚠️❗ ⚠️❗ ⚠️❗ ⚠️❗ ⚠️❗ ⚠️❗ ⚠️❗ ⚠️❗ ⚠️❗ ⚠️❗
Both methods should be used complementarily in a secure package.
Filling – stability through gap management
Filling means closing gaps within the packaging. The aim is to fix the packaged goods so that they cannot move during transport. Filling ensures stability in the carton, especially for robust, less impact-sensitive products – such as textiles, plastic housings or printed products. Typical filling materials are paper fillers, packaging chips, air cushions or foam flakes. Although they dampen slight movements, their main purpose is to block the product in the outer carton and thus prevent it from shifting.
Definition: Filling refers to the filling of cavities between the product and the packaging wall in order to minimise freedom of movement.
- Objective: Transport safety by blocking movement within the outer packaging.
- Application: Especially for light, robust products.
- Materials: Paper fillers, chips, air cushions, foam flakes.
When is filling sufficient?
- For impact-resistant or robust products.
- If the packaged goods are not sensitive to vibration or pressure.
- For bulky, light or angular products.
Suitable filling materials & their properties
Tip: Stuffing material must be stuffed firmly enough to prevent movement – too little material = high risk of damage.
Material | Material properties | Ideal for |
---|---|---|
Paper filler | Recyclable, flexible dosage, shock-absorbing | Books, textiles, cardboard goods |
Packaging chips | Volume levelling, antistatic available | Electronics, plastic parts |
Air cushions | Lightweight, space-saving, good protection against movement | Standard packaging in e-commerce |
Foam flakes | Reusable, precise filling | Small components, laboratory equipment |
Filling techniques – Physically explained
Bulk filling
Bulk filling uses loose materials such as packaging chips, foam flakes or crumpled paper. crumpled paper are inserted into the shipping carton to surround and stabilise the product. This technique is based on the principle of displacement: The space around the product is filled with loose material, which is intended to reduce movement inside the carton.
However, this method has one significant disadvantage: The kinetic energy generated by an impact when the package is dropped, for example, is not effectively absorbed – it can continue to be transferred to the product. If too little bulk material is used or it is distributed unevenly, there is a risk that the product will shift during transport. This can lead to damage – especially with more sensitive goods.
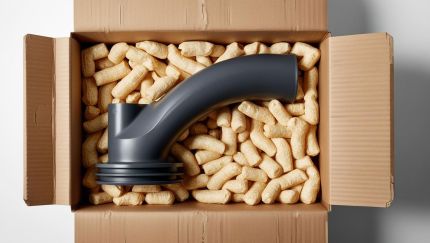
This method is therefore primarily suitable for robust products with low protection requirements, e.g. plastic parts or printed products. A sufficiently high degree of filling is important in order to completely prevent freedom of movement.
- Example: Chips or paper are loosely filled into the carton.
- Physical effect: Displacement → the product is blocked, but the kinetic energy is largely retained.
- Risk: If there is too little material, the product can move = impact transfer.
In this context, another physical phenomenon comes into play, which we will take up here:
The Brazil groove effect – and its relevance for filling and padding
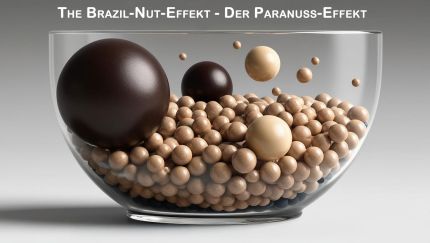
The Brazil-Nut-Effect (BNE) describes the physical phenomenon in which larger or lighter particles move upwards in a bulk material, while smaller or heavier particles sink into the spaces between them – triggered by vibration, shaking or impact movement. Typical (and eponymous) example: In the muesli mix, the large Brazil nuts “migrate” to the top even though they are heavier – simply because smaller particles settle into the gaps when shaken and displace the large particles upwards. Principles such as:
- Percolation (small parts slide downwards),
- Convective flow (through movement within the medium),
- and volume displacement.
This phenomenon has nothing to do with impact transfer in the classic packaging sense. Rather, it occurs with loose bulk goods under repeated movement (e.g. when transporting granulates or small parts).
- Impact transfer = transfer of a mechanical impulse to the product → e.g. through an impact.
- Brazil groove effect = sorting mechanism for bulk goods → large parts move upwards when vibrated.
In these packaging situations, the Brazil groove effect is relevant if :
- loose fillers (such as packaging chips, paper flakes or foam granules) are used,
- the product is not fixed, but “floats” in a sea of filling material,
- there are repeated shocks, jolting movements or vibrations during transport,
- the packaged objects have different densities or size ratios.
What can happen?
- Lighter products (e.g. plastic parts) “float” upwards and lie directly under the carton surface after transport.
- Heavier individual parts (e.g. spare parts or appliances) sink to the bottom – often without sufficient padding.
- The originally homogeneously packaged product lies exposed, unprotected or off-centre after transport – impact resistance is therefore no longer guaranteed.
How can the Brazil-nut effect be prevented?
To systematically avoid the ESD during filling and padding, packers must rely on structuring, space-preserving and fixing techniques. Here are the most important measures:
- Refrain from using pure bulk material for sensitive products: Packaging chips and loose cushioning materials should not be the sole protective measures if the product is lightweight or contains components of different sizes. A structured structure is required, especially for high-quality goods or combined packaging (e.g. cable + power supply unit + accessories)
- Centring using moulded parts or inserts: Use cardboard web inserts, foam inserts or corrugated cardboard moulded parts to mechanically secure the product. These prevent the product from floating or sinking in the bulk material.
- Composite packaging: Wrapping + filling: The combination of wrapping with paper or bubble wrap plus moderate filling of the space prevents the product from migrating. The wrapping gives the product a closed shape and increases friction – this prevents it from “slipping through” into cavities.
- Segmentation of the packaging space: The carton is divided into defined zones – either by multi-part inserts or by layered packaging (e.g. carton with intermediate layer, lid padding, base padding). This mechanically prevents bulk material migration.
- Combination of filling & targeted cushioning: While the filling material prevents movement, targeted padding at corners or sensitive areas ensures that no damage occurs even with minimal migration. This redundancy is recommended for long transport routes.
Wrapping with filling material
A very simple but effective technique is to wrap the product with packing paper or thin kraft paper. This involves wrapping the product completely before placing it in the box. This creates a certain cushioning effect on the surface, while at the same time the product is centred in the box.
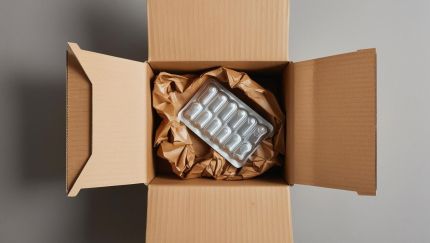
In physical terms, this is a hybrid between filling and light cushioning: the wrapping not only ensures that the product hardly moves in the box, but also absorbs light shocks or friction. However, this method is not suitable for heavy or shock-sensitive products, as paper does not offer any significant shock absorption.
It is particularly suitable for short shipping distances and for less sensitive goods such as textiles, plastic packaging or advertising materials.
- Example: Wrapping a product with wrapping paper.
- Effect: Combination of filling and light cushioning.
- Application: Less sensitive products, short distances.
Chamber formation through air cushions
Modern shipping solutions often utilise air cushions that are positioned around the product. This technology is based on the principle of elastic expansion: the air cushions adapt to the shape of the product and generate a restoring force through their internal air pressure, which effectively blocks movement.
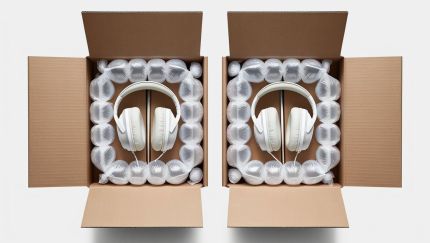
In physical terms, air cushions act like an elastic barrier that encloses the product on all sides and largely prevents movement during transport. At the same time, they provide a certain buffer zone that can absorb minor shocks.
A major advantage is that air cushions are very light, space-saving and often recyclable. This method is ideal for standardised shipping goods in e-commerce, especially for medium-sized, insensitive products where protection against changes in position is more important than shock absorption.
- Products are held in place by air cushions.
- Effect: Movement is blocked by elastic expansion (restoring force).
- Advantages: Lightweight, recyclable.
Cushioning – The airbag for your goods
Cushioning, on the other hand, has a different purpose: shock-absorbing material is used specifically in sensitive areas of the product – such as corners, edges or sensitive surfaces. This prevents shocks, vibrations or pressure peaks from being transferred to the product itself. This technology is essential when shipping fragile, high-quality or sensitive goods such as glass, electronics or precision parts. Materials such as bubble wrap, foam profiles, paper padding or customised packaging foam are used for this purpose.
Definition: Padding refers to the targeted insertion of shock-absorbing material around sensitive areas of a product to protect it from shocks, vibrations or impacts.
- Objective: To protect the packaged goods from mechanical stress.
- Application: for sensitive, fragile or expensive goods.
- Materials: bubble wrap, foam profiles, foam sheets, paper padding, packaging foam.
When is padding indispensable?
- For fragile, sensitive or high-quality products
- For long transport routes or reusable packaging
- If impact or pressure loads are to be expected (e.g. palletising, lorry loading)
Suitable cushioning materials & their properties
Material | properties | Application |
---|---|---|
Bubble wrap | Shock-absorbing, lightweight, various thicknesses | Glassware, cosmetics, technical products |
Foam padding / PE foam | Resilient, vibration-absorbing, dimensionally stable | Electronics, machine components |
Foam profiles | Edge protection, selective protection, easy to fit | Frames, displays, metal parts |
Paper padding (e.g. RAJA) | Sustainable, powerful, mouldable | Heavy or angular products |
Packaging foam (PU) | Customised, ideal for series shipping | Medical and laboratory technology, measurement technology |
Corrugated cardboard padding | Shock-absorbing, recyclable, inexpensive | Universal padding, intermediate layers |
Upholstery techniques – Physically explained
Padding through elastic deformation
This method is used in particular when using bubble wrap, foam sheets or paper padding. The principle is physically clear: in the event of an impact, the air chambers or cell structures in the material deform – and convert the kinetic energy into heat or deformation work.
This effect is comparable to an airbag in a vehicle: the energy is not transferred to the product itself, but “deflagrates” in the material. Depending on the thickness, structure and compression properties of the padding, even strong impacts can be safely absorbed.
This method is ideal for sensitive individual products, electronic devices, glassware or ceramic items that could be damaged by even minor shocks.
- Example: bubble wrap, foam materials.
- Principle: On impact, energy is absorbed by deformation of the air chambers or foam cells.
- Comparison: Like an airbag in a car – the kinetic energy is converted into heat.
Shock decoupling through distance
A particularly effective cushioning technique is to keep the product in a kind of suspended state within the shipping packaging – usually using double-walled constructions with a cavity or defined buffer zone. This means that the energy acting on the parcel does not hit the product directly, but is first absorbed by the outer layer.
Physically, this technology works by delaying the transfer of force over time: The outer shell deforms first, and by the time the energy reaches the actual product, it has already been partially reduced. This process is ideal for highly sensitive shipping goods, for example in medical technology, laboratory equipment, precision sensors or cameras.
However, it is more complex to design and usually more expensive to implement – and is therefore only used for high-quality products with high protection requirements.
- Example: Double-walled packaging with a buffer zone.
- Effect: The product floats freely inside – energy only reaches the outer layer.
- Ideal for glass, electronics and precision parts.
Zone-specific padding
Not every product is equally sensitive – it is often certain areas such as corners, edges or fragile structures that are particularly worth protecting. This is precisely where the technology of zone-specific padding comes in: With the help of foam profiles, edge protection or punched padding, protective material is applied specifically where the risk of damage is highest.
The advantage lies in the material efficiency: instead of wrapping the entire product, protection is only applied where it is really needed. This reduces volume, costs and material usage – while providing a high level of protection.
This method is particularly suitable for frame constructions, displays, industrial workpieces, monitors or housing components where the surfaces are robust but the structural areas are sensitive.
- Example: Foam profiles on corners and edges.
- Effect: Concentration of protection on the most vulnerable areas.
- Application: Monitor, frame, workpieces.
Practical examples: How to combine correctly
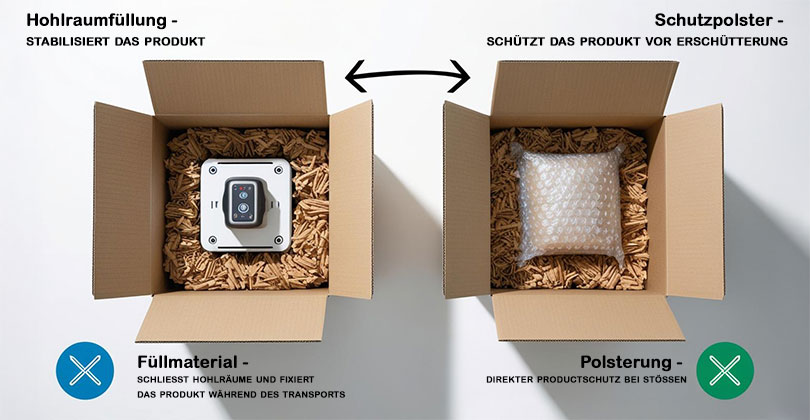
Example 1: Dispatch of Bluetooth headphones
Filling: Air cushions prevent movement in the outer carton.
Padding: Bubble wrap directly around the product.
Example 2: Delivery of a spare part for mechanical engineering
️ Filling: Paper filler or foam flakes for fixation.
️ Padding: PE foam profiles in exposed areas.
Example 3: Glass bottle in e-commerce
Filling: Packaging chips in the dispatch box.
Cushioning: Bottle in paper padded envelope or bubble wrap.
Advice from a professional?
Do you regularly ship sensitive products and want a customised cushioning solution? RAJA offers over 65 years of experience, a wide range of products and personalised advice for your packaged goods.
Contact our packaging experts – we will analyse your processes and optimise your shipping packaging.