Safety in the warehouse: this is a subject that requires a considerable amount of time from the logistics manager, and involves a multitude of key details to be implemented.From the key equipment to be installed to secure assets and goods, to the processes and tools to reduce human risks in the warehouse, discover here a summary of the good logistics safety practices to adopt
- Implementing the basics of warehouse security
- Optimise the structure of your warehouse
- Secure the risk areas of the warehouse
- Keeping your operators safe in the warehouse
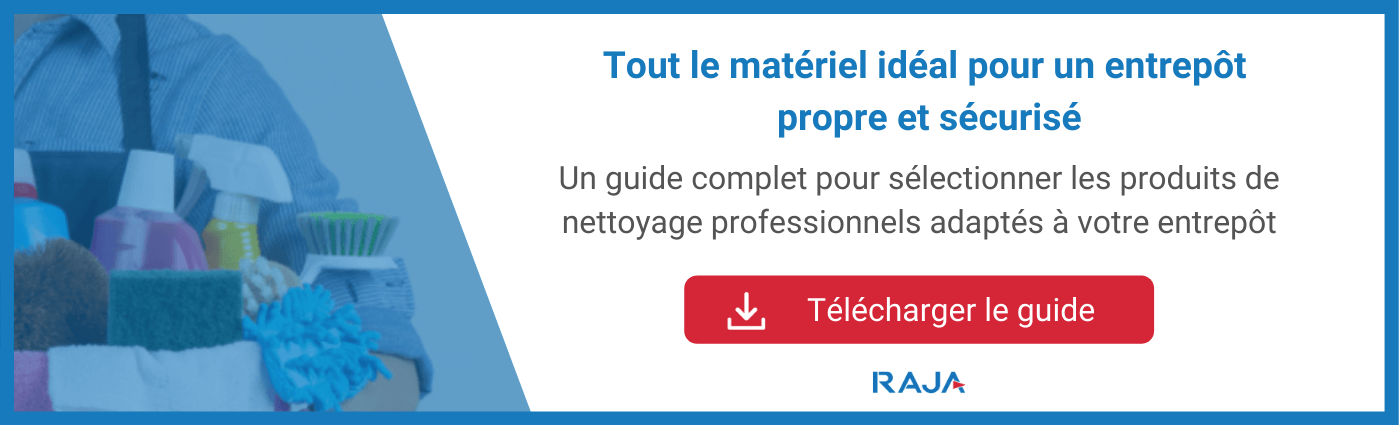
Mettre en place les basiques de la sécurité de l’entrepôt
Dans un premier temps, il convient de se rappeler quelques éléments basiques de sécurité de l’entrepôt. En tant que spécialiste de la logistique, ceux-ci vous seront sans doute déjà familiers… mais une piqûre de rappel ne fait jamais de mal.
Avez-vous l’autorisation d’exploitation de votre entrepôt ?
Pour un entrepôt en règle avec la législation française, vous devez disposer d’une autorisation d’exploitation, à demander auprès de la préfecture de votre région.
Avec cette autorisation viennent un certain nombre de contraintes, et notamment des contraintes en termes de distance entre l’enceinte externe de votre entrepôt et les zones qui l’entourent. Ainsi, votre entrepôt devra respecter une certaine distance avec les zones d’habitation, les bassins et voies d’eau, les établissements publics comme les éc
- Fire systems and processes
- Warehouse waste management
- Current storage rules
- Employee evacuation rules
- Waste water disposal and recovery
- Accessibility of emergency services..
make sure your warehouse is classified in the right category to ensure that it is safe and complies with current standards.
Do you keep a record of the materials you store?
If the warehouse is inspected, you will need to provide the person in charge with a record of the materials stored. This record should clearly show..
- The nature of the products stored, and their specificities
- Their location in the warehouse
- The potential risks associated with them
make sure you keep this record up to date with the new products that are regularly included in your stock.
Optimise your warehouse structure
A well secured warehouse is one that is streamlined in structure and storage, and complies with regulations. Find out what you need to put in place within your structure to minimise risk
Remember: The warehouse safety criteria described here are the responsibility of the operator and not only should they be in place, but their viability and effectiveness (including that of the equipment) should be regularly inspected and optimised. |
what are the key security features of your warehouse?
While some specific warehouses will need to tailor their security features to the types of products stored, the law requires every storage facility to have some basic security features in place. Consider the following..
- Check that the floor is watertight, to prevent soil and water pollution.
- Place the boiler room in a dedicated room, or isolate it from other parts of the building with a safety lock.
- Install emergency exits every 50 metres.
- Installa ventilation system to ensure optimum air quality, but the exhausts from this system should be located away from potential residential areas.
- Equip the warehouse with a system for collecting and treating the wastewater that your business produces.
- Protect the lighting from shocks and overheating, to avoid concerns about fire.
if you have ticked all the boxes in this checklist of essential warehouse safety criteria, you are in compliance with the main standards in force.
Have you created a lane dedicated to machinery?
French law also requires all warehouses to create a “machinery” lane. Its objective is to facilitate the flow of goods inside the building. This lane must meet specific criteria, as follows
- A width of 6 metres
- A clearance height of at least 4.5 metres
- A slope of less than 15%
this “machinery” lane must remain free at all times, to facilitate circulation in the event of an incident that jeopardises the safety of the building and its operators (fire, collapse, etc.).
What signage to ensure safety?
When you talk about making the flow of goods in the warehouse safe, you also talk about the installation of appropriate signage. Whether or not your activity requires the use of handling machines, signage makes it possible to avoid the risk of collisions, and therefore to reduce accidents in the warehouse. In particular, think about positioning signage at key points in your structure..
- Ground marking tapesin order to delimit the paths dedicated to the different flows, or to indicate specific zones for each phase of your order preparation
- Safety mirrorsin areas where flows cross, to improve visibility in the warehouse and avoid blind spots during traffic
- Emergency and evacuation signsat key points in case of accident or risk
- Signs indicating safety instructionsat strategic points: entrance to the warehouse, exit from rest areas or changing rooms, etc
- Floor trestles if it is slippery (especially after cleaning the floors)
once you have put up your warehouse safety signage, your operators will be able to apply the key safety measures with complete peace of mind.Securing
risky areas of the warehouse
Not all areas of the warehouse present the same degree of risk of accident or incident. Some of them deserve special attention: find out here which ones, and the few key measures to take to increase their safety.
Pallet racks and high shelving
As soon as loads (more or less heavy) are stored at height, the risk of collapse and therefore of an accident increases. Pallet racks (which enable pallets to be stored) or high shelving are therefore particularly risky areas in the warehouse. To avoid any problems, make sure that you..
- Anchor your shelving and racks in the concrete floorif the floor is slippery (e.g. after cleaning the floors), as required by the safety standards in force from a certain height and weight.
- Install reinforcing feet and crosspieces on your racks to optimise their overall stability.
- Respect the maximum load of the racks and shelving indicated on specific labels.
- Inspect these installations daily. They may deform slightly when heavy loads are placed on them, but should return to their original shape when these loads are removed. If this is not the case, make sure they are replaced, with a better estimate of the maximum load required.
- If necessary, choose safety ladders or stepladders thatcomply with the standards, to minimise the risk of operators or goods falling when handling them.
of course, such installations require specific training for the operators who have to use them. Regularly remind your teams of the safety rules associated with them.
Mezzanines with posts
To free up floor space and optimise storage space, many logistics managers decide to organise their warehouse with mezzanines mounted on posts. If you are planning to set up such an installation, make sure that it is..
- Be sure to seek expert advice on the best equipment to choose.
- Ensure that safety barriers areinstalled around the poles and for access to the mezzanine floor.
- Provide the area with signs specific to the installation, highlighting its dangerousness and the rules for using handling equipment in the area.
les chariots élévateurs
Les chariots élévateurs peuvent sembler être des machines simples à manier, à première vue. Cependant, les risques de sécurité dans l’entrepôt qui y sont liés sont bien réels, et doivent être évités grâce à une formation spécifique.
Vous le savez sans doute : seul un cariste, formé aux bonnes pratiques liés aux chariots élévateurs, peut manipuler l’engin. Pour l’aider à bien réaliser la manutention à l’aide de la machine, veillez à aménager correctement la zone de l’entrepôt concernée, en laissant assez d’espace disponible à l’engin pour circuler.
Vous souhaitez tout savoir sur les grandes règles du stockage en entrepôt, pour réellement rationaliser votre espace ? N’hésitez pas à télécharger notre guide dédié au sujet, qui vous éclairera sur les différentes méthodes et règles de sécurité à envisager.
Assurer la sécurité de vos opérateurs dans l’entrepôt
Comment parler de sécurité dans l’entrepôt
sans parler
- The right safety footwear: Not only should it comply with ISO 20345 standards, but it should also have a protective toe cap and a suitable sole to ensure comfort when standing. To help you choose the right type of safety footwear, take a look at our guide to choosing safety footwear.
- The right work clothes: Depending on whether your workers handle hazardous materials (aerosols, particles, liquids, sprays, etc.), you will need to select clothes that are more or less protective. Be sure to comply with the 1992 European directives on the degree of personal protection provided.
- There are several types of gloves, depending on the level of protection you need to provide your operators: short-use gloves to avoid contact with chemicals or micro-organisms, anti-cut gloves to limit the risk of cuts, dexterity gloves to avoid mechanical risks, etc. While the choice of the type of glove is crucial, you should also make sure that you choose the right size for your operators. To choose the gloves that are best suited to your needs, please take the time to consult our guide to choosing gloves.
How to optimise warehouse hygiene?The Covid-19 crisis of 2020 proved it more than ever: the warehouse is an area where hygiene must be impeccable, both to limit the spread of diseases between operators and to ensure optimal storage quality of goods. If you are looking for best practices to ensure warehouse hygiene, check out the article on the subject, which RAJA developed during the Covid-19 crisis, but which is still as relevant as ever for warehouse safety. |
how to fight against Musculoskeletal Disorders (MSDs)?
Musculoskeletal disorders are one of the major concerns that a warehouse can encounter. Reduced quality of life at work, lower productivity, and an average cost of €21,512 per year to a company: it is in the best interest of logistics managers to avoid their pitfalls. So how do you go about it? First of all, you need to know how to identify MSDs throughout the supply chain. There are three main sources of MSDs
- Biomechanical factors, such as repetitive movements, static work, excessive strain, extreme joint positions, etc
- Psycho-social factors, such as stress related to time management, or lack of support from teams and managers
- Organisational factors, including poorly organised schedules with difficult deadlines and insufficient recovery time
these MSD risk factors result in work-related accidents (sprains, dislocations, fractures, contusions, falls from heavy packages, exposure to dangerous products, etc.), but also in physical constraints whose effects occur over a longer period of time (vibrations from self-propelled forklifts, carrying heavy loads, prolonged standing, forced movements of certain parts of the body, etc.). To limit MSDs, and therefore increase safety in the warehouse, think about implementing a genuine prevention methodology. It is recommended to..
- Start by eliminating biomechanical factors, which can be done by installing specific equipment that limits the most intense physical strain on operators.
- Next, identify the organisational and psycho-social factors that can create MSDs. For example, training operators in the tools that are supposed to alleviate drudgery in the warehouse is often overlooked.
- Everyone must be constantlyaware of the risk factors and the symptoms of MSDs that can occur.
What are the main symptoms of MSDs?Know this: 4 types of health concerns account for 75% of occupational diseases. Know how to recognize them
|
in addition to this methodology, there are a number of elements that can help you to significantly reduce drudgery in the warehouse, and reduce the risk of MSDs. In particular, consider..
- Equip yourself withan automaticwrapping or filming machine if your operators palletise a significant number of pallets per day.
- Optimise packing stations so that they are more ergonomic and all the equipment needed for order picking is within the operators’ reach. For more advice on this subject, consult our guide dedicated to the subject.
- Equip your operators with the right handling equipment: from pallet trucks to variable height trolleys, and even rollers for loading parcels into trucks, there are plenty of ways to lighten the load your operators have to carry on a daily basis.
- Consider installing anti-fatigue mats in the warehouse. When you know that 49% of warehouse workers work standing for more than 20 hours a week (according to a study by the INRS), it becomes important to make the static standing posture as painless as possible for your employees.
with this comprehensive guide, you are ready to face all safety risks in the warehouse, both for your goods and for your teams. Find all RAJA products related to safety, hygiene and maintenance here