Order picking in a logistics warehouse can be a real challenge. At the heart of this daily challenge, which e-tailers know well, there is one key stage that makes the difference at the end of the packing chain: picking.The key to an optimised picking method
- Increased productivity of your operators
- Improved management of physical flows in the warehouse
- Optimal safety for your teams
- A reduction in Musculoskeletal Disorders (MSD)
this article reveals all the keys, from the storage method to the necessary equipment
- What is logistics picking?
- What are the different existing picking methods?
- Which storage method for optimal picking?
- What is the difference between picking in a large warehouse and picking when starting out in e-commerce?
- What equipment is needed to optimise your picking?
- How to create picking lists for your operators?
What is logistics picking?
Picking is a key moment in order picking: the moment when the picker goes to the warehouse to collect the items in an order, to gather them in one place so that the parcel can then be prepared. Picking is a key stage in order picking and deserves to be optimised, just like the storage, packaging and dispatch preparation stages. The aim when you optimise your picking phase is to limit the number of movements of operators in the warehouse, to reduce order picking time and facilitate handling
Attention: warehouse picking ≠ shop pickingStore picking, also known as “point of sale picking”, requires operators to prepare orders in the shop, from its shelves or stock, in order to offer home delivery or a drive-through service. This isa much simpler picking method than warehouse picking, since packaging is much easier. When picking in the warehouse, one of the operators’ primary aims is to package the goods securely, in order to avoid breakage, and therefore the return of products. The storage of point of sale picks is also quite different, since it is separate from the logistical challenges of a stock, and is therefore much less dynamic. |
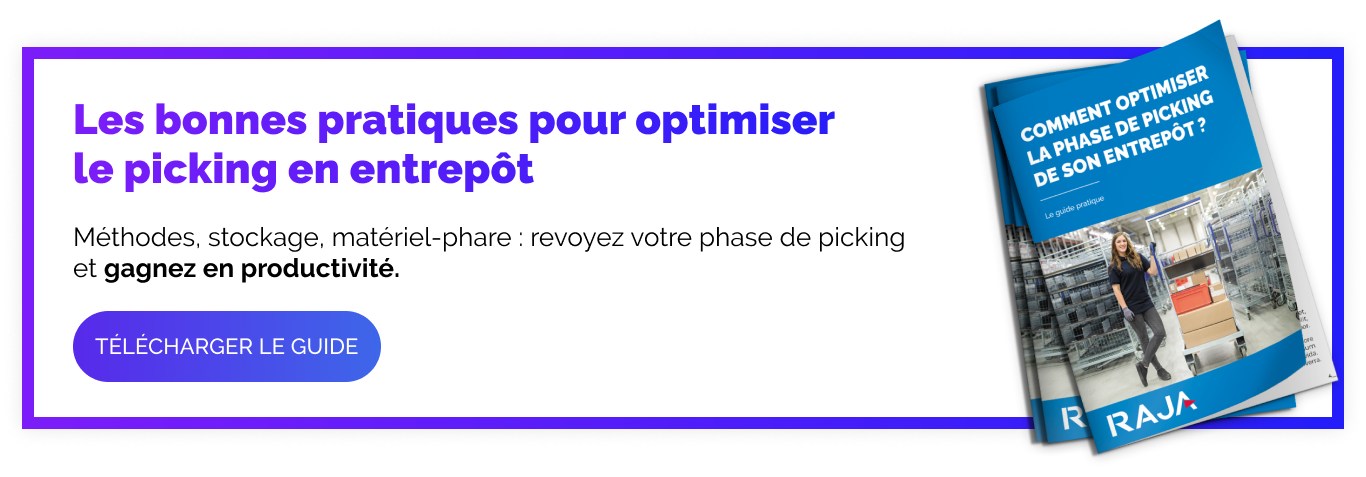
Quelles sont les différentes méthodes de picking existantes ?
Pour commencer à optimiser votre phase de picking, il vous faut choisir la méthode qui convient le mieux à votre activité et à votre entrepôt. Découvrez ici 4 méthodes de picking “homme vers article”.
Le picking en “pick and pack”
La méthode “pick and pack” demande au préparateur de commande d’aller chercher les produits à inclure dans le colis, puis de les emmener vers la zone d’emballage, pour ensuite aller chercher les produits d’une autre commande.
Un même opérateur peut également, lorsqu’il prend en charge plusieurs commandes, aller récupérer l’ensemble des articles de ses différentes commandes, pour les répartir ensuite sur la zone de colisage.
Le picking en “pick and pack” est particulièrement adapté aux entrepôts envoyant peu de colis dans une même journée
,
puisqu’il s’agit d
’
une méthode assez peu rapide.
Le picking en “ put to light
- Increased work rate, which can overload operators
- Increased operator stress, with a feeling of dehumanised work
- Decreased awareness of effort, which increases the risk of collisions in the warehouse for example
- Potential hearing problems..
to make a conscious decision to use Voice Picking, don’t hesitate to consult our article on the subject: For or against Voice Picking?As you have seen, some picking methods require high equipment costs and computerisation of the warehouse. That said, the ROI of these methods is quickly realised, with a warehouse that gains in productivity and a reduction in the number of errors during the process.
Which storage method for optimal picking?
Optimised picking phases require an appropriate storage method. Only an optimal storage method will enable you to reduce picking time and the efforts of your operators. Discover the 3 storage methods to choose from in order to set up a really clever picking strategy.
The ABC method: Activity Based Coating
The ABC method
is
a
method
that is used to assess the efficiency and effectiveness of a warehouse
How to ensure the safety of operators during picking?Having a good stock management method, linked to its picking method, is not enough to ensure the safety of pickers during the phase of picking products from stock. Think in particular of..
if you would like to know more about safety in the warehouse, please read our article “How to ensure the safety of your employees and your goods” |
what is the difference between picking in a large warehouse and picking when you are just starting out in e-commerce?
Whether you are just starting your e-commerce business or you are already in charge of large-scale logistics, it is always interesting to look at existing picking methods.
An example of picking in a large warehouse: Amazon Prime
Have you ever seen what the picking phase looks like in the Amazon Prime warehouses, which require the e-commerce giant to deliver ordered products within 24 hours? The process is interesting, even inspiring
amazon Prime relies on new technologies, especially data. On the surface, it may seem that the products are stored in a totally disorganised manner, but it is actually technology that manages the operators’ picking
- They scan the item they are storing at a specific location in the warehouse
- The software records the location of the product
- The same software gives the operators in charge of picking the product the location where they must then go to collect it
- It also determines the optimal path to pick the product in the warehouse, to limit
- the travel time of the operators
inspiring, isn’t it?
A picking and storage method for small warehouses
Although the example of Amazon Prime is inspiring, it is not applicable to small warehouses, especially those just starting their e-commerce activity. If you have a small order preparation team and manage a few dozen orders per day, you should favour a “pick and pack” picking method, where each of the operators takes care of one order in its entirety, right up to the packing and dispatch phase. In terms of storage method, think about organising your warehouse well according to..
- The location of the items, and how often they are purchased. ABC is a good starting point, unless you sell perishable products, in which case FIFO is preferable.
- The weight of the products: make sure that your operators pick the heaviest products first, by putting them at the bottom of your shelves.
with good organisation from the outset, and a suitable picking method, you will be able to professionalise your stock more easily once it has grown. Also make sure you optimise your order preparation table, which is the key place from which your parcels leave, and which requires real organisation in order to be productive. cta id=’debfe4b2-cf25-4088-8cf4-a11677baa0f2′]
What equipment is needed to optimise your picking?
As you can imagine, optimising your picking also means choosing the right equipment to give your operators the chance to be more productive, in complete safety. Depending on whether you manage a BtoB or BtoC warehouse, this equipment will be different
What are the differences between BtoB and BtoC picking?In BtoC, orders are generally smaller than in BtoB, where delivery and storage are often done in the form of pallets. It can also be observed that picking distances in BtoC are often longer, that the flow of products in the stock is often based on seasonality, and that order preparation requires more meticulousness and attention. Indeed, the BtoC consumer is more likely to complain about a poorly packaged or poorly-prepared order than a company. In BtoC, picking is therefore a matter of customer satisfaction, and therefore requires even more particular attention. |
picking equipment for BtoB
In BtoB, your order pickers are often faced with large loads to store and transport from one side of the warehouse to the other. The equipment dedicated to BtoB picking will therefore have to follow very specific safety instructions. In particular, make sure you choose..
- The right shelving: galvanised steel for loads of up to 170 kg per shelf, chipboard for heavy products, or specifically designed for pallets: it’s up to you to decide which one is best suited to your business. Also take the time toanchor your shelving in the concrete floor, and to fit reinforcing feet and crosspieces on it, for legal security.
- Storage systems for your shelving: while folding bins save space in the warehouse, horizontal or side-opening crates allow easy access to the products, think of spout bins for smaller goods stored in bulk.
- Optimal labelling: Identification signs to help your operators find their way around the warehouse, as well as label holders(adhesive or magnetic) are essential.
- Theright handling equipment: to carry heavy or light loads, your pickers will need manual or electric forklifts and tables, as well as pallet trucks and stackers adapted to their needs.
Picking equipment for BtoC
On the BtoC side, the concern about loads is less important: it is more a question of creating an optimal organisation for the operators, so that they can pick the products in an efficient way. Think in particular of choosing, among the essential equipment for picking in BtoC..
- Accessible, versatile and robust shelving on a human scale, allowing you to adapt the organisation to your seasonal needs. If you need to create racks that are higher than human height, add ladders or forklifts.
- Bins and crates to organise the racks: folding bins, totes, horizontal or side opening crates… Choose different colours for each type of product stored, to help your operators to see the differences in the warehouse.
- Trolleyschoose them so that they are suitable for multiple uses.
Think about organising the circulation in the warehouseIn BtoB as in BtoC, your operators need to be guided safely to the picking and order preparation areas, so think about..
|
how do you create picking lists for your operators?
The last step in truly managing your logistical picking from A to Z is to create picking lists (also known as “picklists”) that will make your pickers’ work easier. On these lists, whether they are printed or can be consulted on a tablet in digital mode, remember to indicate all the essential logistical information, namely
- The order number, to differentiate orders from each other, either during the picking phase or later, if a picking problem occurs.
- The area where the product is to be picked up. Make sure that the location is indicated precisely, to facilitate the picking phase for your operators.
- The item code, or Stock Keeping Unit (SKU): this element, indicated precisely on your shelves and/or racks, helps to limit the error rate during the product picking phase.
- The quantity of products to be picked: this is an extremely important point, especially in B2B, where the volume of products to be picked is often greater.
- Some information about the customer, such as name and delivery address.
make sure that these picking lists are as simple as possible, and that they only contain information that is useful to the operator during order picking. These documents should help him to trace and trace back any errors in the picking chain. Well done: you have all the tips you need to implement an effective picking strategy, adapted to the needs of your logistics warehouse and your operators