Being responsive to customer orders is essential to building customer loyalty. Yet many warehouses waste time by not automating certain tasks. Getting the right tools and getting rid of time-consuming processes will give you a productivity boost.
In this article, you will find all the tips you need to speed up your order processing and picking in every phase of your supply chain.
This article was updated in October 2020.
Diagnose bottlenecks in order processing
While the definition of the term “order processing” is fairly straightforward, the sheer number of tasks it encompasses requires some thought as to its definition.
What is order processing?
Order processing is the entire process that starts when a customer makes a purchase and ends when they open the package containing their goods.
The steps leading to delivery are not necessarily the same from one company to another, so you need to ask yourself a simple question: What in your business is an efficiently processed order?
The answer is that in the majority of cases it is a promise of delivery that is kept, and a loyal customer.
The stages of order processing
As we have seen, order processing is divided into clearly separated tasks, from the customer’s purchase on the site to the delivery of the product.
Let’s take a look at the specific tasks involved:
- Checking payment and delivery address: basic, you need to make sure that the customer is solvent and that no mistakes have been made when entering the delivery address.
- Ensure stock availability: sometimes the right IT tool for automated stock-taking is not available, an obstacle that can waste precious time in order to process orders efficiently.
- Picking: this stage consists of retrieving the ordered items from the shelves.
- Packing: the items ordered must be carefully packed by the order picker in order to guarantee safe transport. This is the very definition of order picking.
- Dispatch: the parcel is picked up by your carrier and transported to its destination.
- Manage invoicing: this involves issuing invoices for customer purchases.
- Managing returns and after-sales service: sometimes things don’t go according to plan, and you have to deal with a customer who is not satisfied with your product or its delivery. This is a critical step, and it has a huge impact on how customers perceive you. Again, tools affect your response time.
You should now be able to identify which stage of the order process can be improved in your company.
Often the bottlenecks are in the software used by the companies, which is too old, not functional enough, not up to date…
A poor organisation of the logistic chain is also regularly pointed out.
How to optimise order processing?
An exhaustive knowledge of these order processing processes is essential for optimisation.
Follow the steps with a magnifying glass, control the preparation of the orders, and identify the breaks, the badly oiled gears, which make you lose time, and therefore efficiency.
How can you avoid the obsolescence of your tools?
Optimising your order processing can save you 2 to 3 minutes per order, which is an undeniable gain that will allow you to send out more orders in the long term.
The right reflexes to optimise order preparation
The main areas for improvement are in your supply chain.
- Is your product classification optimal? Why not opt for an ABC type of referencing, when a large proportion of your orders correspond to a small group of products? This would make picking tasks much easier.
- Can your packing phase be unbridled, for example by using pre-cut cartons, instant crates, or bubble wrap dispensers that save you from having to cut the cartons manually?
- Could a computerised stock management system prove to be a vital time-saver that would help you avoid stock-outs?
Find out more tips for order pickers.
It takes a lot of work to revise your organisation.
Order processing processes can change, especially when the order book fluctuates.
Too many orders? Review your order processing to avoid drowning
Your order book is exploding – good for you! But what about your dispatch management?
Just-in-time delivery is great for your company’s finances, but can be a real headache for your operators.
The more your business grows, the more you need to use professional tools to save time and not waste it.
If you have already implemented the tips and tricks to make your logistics operators’ work easier, the adoption of a high-performance web back office is the best solution.
You will then automate many processes, such as the first steps of payment or stock verification, and will be able to concentrate on the essential: meeting your deadlines and the traceability of your orders.
You won’t be taught how to process purchase orders, or how to do professional packaging.
But are you doing it efficiently? That’s what good order processing in logistics is all about.
Identifying which processes can be automated, and being self-critical and adjusting your tools so that you are never overwhelmed by too many orders – a matter of insight, of logic, which could lead you to process between 20 and 30% more customer orders, on a daily basis!
The three key points to remember
- Order processing is all the steps between the customer’s order and the receipt of the product.
- The use of outdated tools, the delay in computerisation or the poor organisation of your warehouses slow down your order processing process.
- Adopting a powerful back-office can help you to better control the preparation of orders.
If you want to go further in optimising your order picking, discover the perfect parcel guide, which will help your logistics teams to better manage the order picking process.
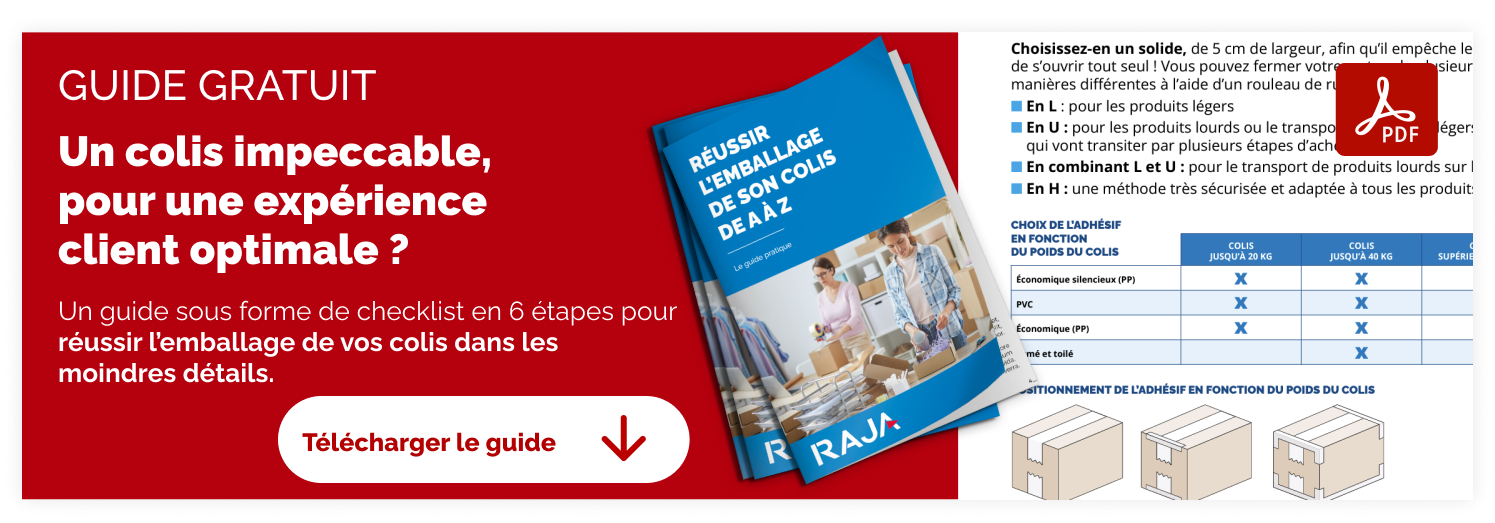