Stock and supply management is a key issue for businesses, particularly in the e-commerce sector. When it’s efficient, you can respond better to customer demand, while optimising your costs. There are various methods and technologies you can use to improve your competitiveness. Find out everything you need to know about stock and supply management in the rest of this article!
- Definition of stock management
- What are the objectives of stock management?
- What are the benefits of stock management for companies?
- The different stock management methods
- Which software, tools and hardware are needed for stock management?
- 10 tips for optimising your stock management
Definition of stock management
Stock management is an essential part of the supply chain. It involves the organisation and monitoring of stocks from suppliers of raw materials and components to a company’s warehouses and points of sale.
It includes a number of important elements, such as
- Demand forecasting
- Replenishment
- Inventory control
- Stock optimisation
- Order management
- Storage strategies
- Data analysis
Generally speaking, there are 8 types of stock:
- Raw materials inventory raw materials required for production
- Semi-finished products: products in the course of manufacture
- Finished goods inventory: products ready to be sold
- Merchandise stock: products intended for purchase and resale
- Safety stock / buffer stock: to compensate for uncertainties in demand and supply
- Seasonal stock: to anticipate seasonal variations in demand
- Speculative stock: to anticipate market fluctuations (price rises, shortages, etc.)
What are the objectives of stock management?
Stock and supply management meets 8 major objectives:
- Cost reduction Reducing costs: storage, orders, purchasing, transport, etc.
- Customer satisfaction by meeting their expectations as quickly as possible
- Optimisation of resources by making efficient use of storage space and human and financial resources
- Streamlining operations by ensuring the efficient movement of stock through the supply chain
- Supply chain responsiveness by gaining the flexibility to react to market fluctuations by adapting strategies
- Continuity of operations by anticipating production interruptions due to supply shortages.
- Order optimisation by adopting the best replenishment methods.
- Reducing losses due to expiry and obsolescence for goods with a limited lifespan
The overall aim is to get the right products to the right place at the right time.
What are the benefits of stock management for businesses?
Optimising your stock management process helps you to meet several major objectives:
- A reduction in storage-related costs Reducing storage-related costs: storage fees, insurance, product depreciation and deterioration, etc.
- Reducing overstocks and stock-outsMaintain optimal stock levels
- Improved customer satisfactionby ensuring better product availability to boost sales
- Optimising delivery timesby ensuring faster dispatch
- Savings on ordersby identifying the best time and the ideal quantity
- More accurate forecastsby analysing data to identify trends and adjust stock levels
- Reduced tied-up capitalby transferring savings to other activities
Effective stock management is therefore an excellent way of improving your production chain, customer satisfaction and cost control.
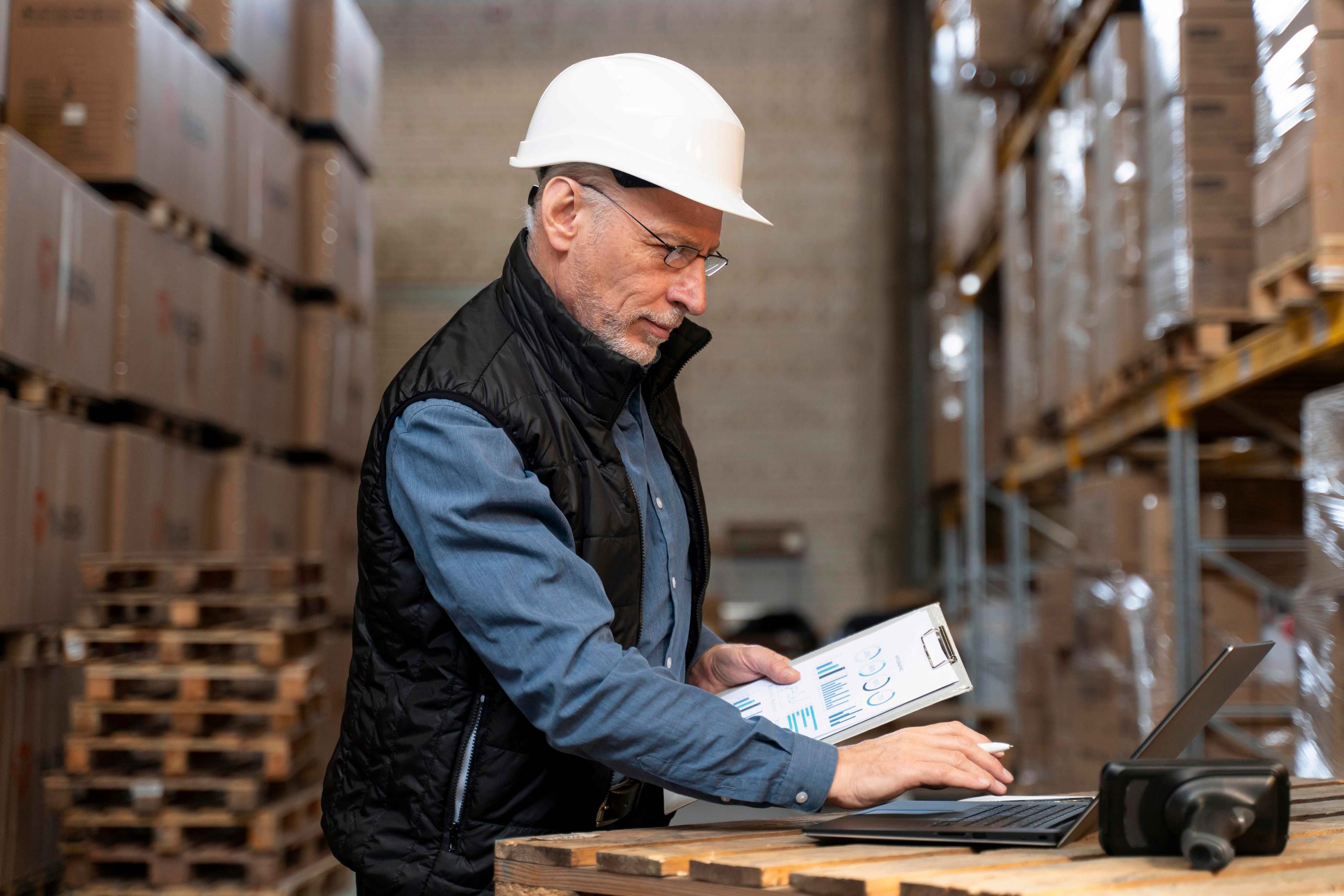
The different methods of stock management
Stock and supply management meets 8 major objectives:
- Cost reduction Reducing costs: storage, orders, purchasing, transport, etc.
- Customer satisfaction by meeting their expectations as quickly as possible
- Optimisation of resources by making efficient use of storage space and human and financial resources
- Streamlining operations by ensuring the efficient movement of stock through the supply chain
- Supply chain responsiveness by gaining the flexibility to react to market fluctuations by adapting strategies
- Continuity of operations by anticipating production interruptions due to supply shortages.
- Order optimisation by adopting the best replenishment methods.
- Reducing losses due to expiry and obsolescence for goods with a limited lifespan
The overall aim is to get the right products to the right place at the right time.
What are the benefits of stock management for businesses?
Optimising your stock management process helps you to meet several major objectives:
- A reduction in storage-related costs Reducing storage-related costs: storage fees, insurance, product depreciation and deterioration, etc.
- Reducing overstocks and stock-outsMaintain optimal stock levels
- Improved customer satisfactionby ensuring better product availability to boost sales
- Optimising delivery timesby ensuring faster dispatch
- Savings on ordersby identifying the best time and the ideal quantity
- More accurate forecastsby analysing data to identify trends and adjust stock levels
- Reduced tied-up capitalby transferring savings to other activities
Effective stock management is therefore an excellent way of improving your production chain, customer satisfaction and cost control.
The different methods of stock management
In addition to the technologies discussed later in this article, stock management requires the implementation of a number of working methods to effectively control stocks and ensure that production lines and points of sale are properly supplied.
Find out which storage method is best suited to your logistics picking.
The ABC method
The ABC method is based on Pareto’s law (also known as the 80-20 law). Goods in stock are classified into 3 categories according to their value or consumption volume:
- Category A Products that leave the warehouse most often (around 20% of the stock quantity for 80% of the revenue generated).
- Category B Products that have an average turnover rate (around 30% of stock quantity for 15% of revenue generated).
- Category C Products that leave the warehouse the least often (around 50% of stock quantity for 5% of revenue generated).
The advantages
- Focus on Category A items to rationalise resources.
- Reduced storage costs and obsolescence risks for C category items.
- A solid basis for making better strategic decisions.
Disadvantages
- Regular updating is required to maintain the relevance of classifications.
- Complexity of use in the case of highly diversified products or products with varied life cycles.
- Factors such as operational criticality and demand variability are not taken into account.
Find out when and how to use the ABC method for your warehouse?
The FIFO method
The FIFO (First In, First Out) method is based on a simple concept: the first items added to stock will be the first to be removed. In other words, the oldest items in stock must be used or sold first.
The advantages
- Minimise the risk of perishable items deteriorating before they are removed from stock.
- Better compliance with accounting principles and standards (GAAP and IFRS in particular).
- A better estimate of the real value of stocks, as more recent items are generally closer to current market prices.
- Greater transparency in tracking inventory and goods movements
- Simple to understand and implement.
Disadvantages
- More complicated management in the case of very high volumes, which will limit and complicate the precise tracking of batches.
- An impact on taxation in times of inflation, as the costs of properties sold are based on older, often lower, costs, which can increase declared income and therefore taxation.
The LIFO method
The LIFO (Last In, First Out) method is also very simple to understand: this time, the last items added to stock are the first to be used or sold.
The advantages
- A better reflection of current market costs, allowing you to visualise more realistic profit margins.
- Tax advantages in times of inflation, as costs of goods sold are based on the most recent prices, which can reduce reported profits. Partly for these reasons, the LIFO method is prohibited by the tax authorities in some countries, such as France.
The disadvantages
- The method is not permitted under IFRS, which limits its use for international companies.
- Greater risk of depreciation or obsolescence of products in stock.
- Administrative complexity for companies managing very high volumes.
The average cost method
The average cost method, also known as the weighted average cost (WAC) method, calculates the value of inventories and the cost of goods sold on the basis of a weighted average of the costs of the items available in stock.
Weighted average cost = (total cost of available inventory / total number of units available)
Each inventory withdrawal is valued at this weighted average cost.
The advantages
- A very simple calculation, suitable for companies with many batches at different costs.
- A more stable and consistent picture of the costs of inventories and goods sold by smoothing out price variations.
- A method widely accepted by international accounting standards (IFRS).
The disadvantages
- Less reliable reflection of costs during periods of sharp price fluctuations.
- Potentially more complex inventory management in the case of products with different lifespans or specific characteristics.
Standard cost method
The standard cost method involves determining predefined costs for products upstream. These are generally based on an analysis of historical costs, economic forecasts and management objectives. They include the costs of raw materials, direct labour and manufacturing overheads.
Standard costs are then compared with actual costs to identify favourable or unfavourable variances and determine their causes.
The benefits
- Increased cost control by quickly identifying where and when fluctuations require corrective action.
- Easier planning and forecasting to establish realistic budgets and financial targets.
- Evaluate operational and management performance by identifying areas for improvement.
- Simplified accounting by reducing the complexity of accounting records.
The disadvantages
- Standard costs can be complex to calculate and need to be regularly updated in line with market conditions
- Management rigidity that limits the company’s ability to adapt to change.
The calendar replenishment method
The calendar replenishment method involves the company ordering fixed quantities of goods on fixed dates. These are generally contracts signed with suppliers, specifying delivery days over the coming months.
It is best suited to companies that consume or sell goods at regular intervals.
The advantages
- Simple to use, with little investment in time and administrative costs.
- Generates savings on bulk or high-volume orders.
- Greater organisational and dispatch reliability for suppliers.
Disadvantages
- Administrative complexity when it comes to changing the order dates in the contract with the supplier.
- Lack of flexibility, making it useful only for products with a high turnover.
The replenishment method
The replenishment method consists of ordering according to the quantity remaining in stock, in order to always return to the maximum stock level defined by the company.
This method is recommended for the most expensive products or those that are perishable and are consumed or sold regularly.
The advantages
- Optimum stock levels at all times.
- Savings by adapting quantities ordered to actual requirements.
- Financial assets are easier to control.
The disadvantages
- A risk of overstocking or stock shortages in the event of unforeseen fluctuations in the consumption or sale of goods.
The point-order method
The point-order method, also known as the “just-in-time” method, involves ordering a fixed quantity at a variable date.
The company first defines its critical stock. When it is reached, an order with a predefined and identical quantity is placed to replenish it.
The advantages
- A method that simplifies the management of irregularly flowing stocks, avoiding overstocking and stock-outs.
- Savings thanks to fewer orders, which means lower logistics costs and a constant amount of storage.
The disadvantages
- Dependence on suppliers’ ability to respond quickly to unexpected orders.
- A need for constant, precise monitoring to optimise the timing of orders.
- A continuous stock safety threshold that involves ongoing costs.
The on-demand replenishment method
As its name suggests, the on-demand replenishment method involves ordering variable quantities on variable dates.
The advantages
- No unnecessary capital expenditure on non-recurring orders.
- More efficient management when the company has no visibility over its order frequency or the quantities it needs in the short term.
The disadvantages
- Complex to use, requiring reliable processes and therefore significant investment in time.
- A more complex relationship with suppliers, who also lack visibility and may find themselves in difficulty when it comes to unexpected orders.
Which software, tools and hardware for stock management?
Essential software for stock management
The stock management table
Companies that don’t have specific business software most often use Excel spreadsheets for their stock management.
However, Excel and its alternatives quickly reach their limits. It lacks automation, which implies a need for very detailed monitoring and regular manual updates.
The Warehouse Management System (WMS)
When the volumes stored are higher, it becomes necessary to equip yourself with software dedicated to this type of operation.
WMS offer a number of advantages, including
- improved productivity
- reduced stock levels
- analysis and forecasting of consumption
- optimisation of storage space
- reduced risk of order errors
Enterprise Resource Planning (ERP)
This type of software complements the WMS, making it easier to monitor stocks and inventories in real time, with a number of advantages:
- a global view and better control of stocks
- optimised flows
- automated replenishment
- analysis of consumption and behaviour
Advanced Planning System (APS)
This tool is designed to facilitate planning, from generation to transmission and distribution. In particular, it enables :
- better organisation
- process optimisation
- improved profitability
The essential tools for stock management
The barcode
In addition to software, it is advisable to implement physical solutions to facilitate stock management.
The barcode equips goods with a unique identification that can include a variety of data: dimensions, weight, storage characteristics, supplier name, quantity in stock, etc.
RFID technology
RFID (Radio Frequency Identification) is a wireless identification and data-sharing technology.
Each item is given a unique serial number and information. When coupled with warehouse management software, it boosts performance tenfold, with improved stock visibility and automated recording of receipts and deliveries.
Picking
Picking refers to the stage during which the picker retrieves the items in an order from the warehouse, putting them together to prepare the parcel.
This is a crucial stage in the supply chain and stock management. Optimising it will save you a lot of time and money in your day-to-day activities.
Find out how to optimise picking in your warehouse!
The picking list
The picking list, or picklist, is a tool that helps to reduce order picking errors. Its role is to explain to pickers which goods to pick for which orders.
It should contain the following information as a priority:
- The order number
- The area where the product is to be picked up
- The product code
- Product name and description
- Quantity to be picked up
- Customer information
Discover our guide to creating efficient picking lists for your warehouse!
Voice picking
Voice picking is order picking by voice. In practical terms, the picker is equipped with a headset and a microphone and is given the picking tasks, the areas where the goods are to be picked, the quantities to be picked, the place where the goods are to be deposited, etc.
However, there is some debate about this automated picking process. It’s important to find out all about the advantages and disadvantages so that you can make the best decision for your particular situation.
Find out all you need to know about voice picking!
Essential stock management equipment
Shelving
Racking allows warehouses to be laid out in a way that optimises stock placement.
There are different types of shelving, such as :
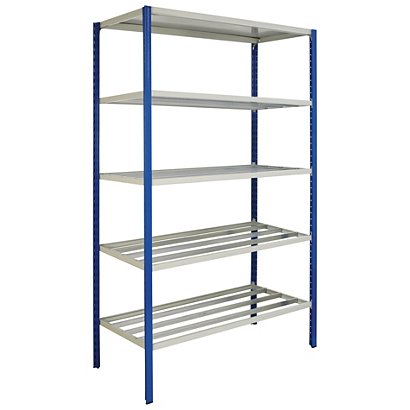
Epoxy steel shelving, for lighter loads such as archives or files.
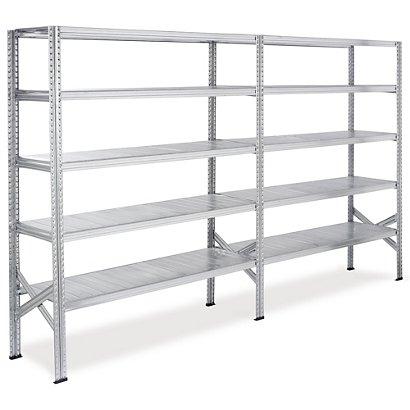
Galvanised steel shelving, for loads between 170 and 200 kg per shelf.

Galvanised steel shelving with chipboard top, for loads of up to 580 kg per shelf.
Choosing the right shelving for your warehouse can sometimes be a headache. Check out our guide to choosing the right shelving!
Bins and totes
Bins can be used to organise shelving, particularly for storing bulk goods.
They come in different formats, such as :
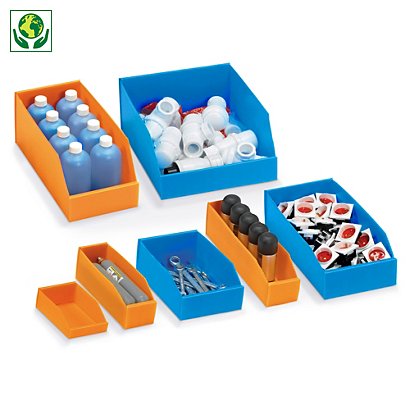
Spout trays made from polypropylene honeycomb to withstand water, grease, chemicals, impact, bending, tearing and temperature variations.
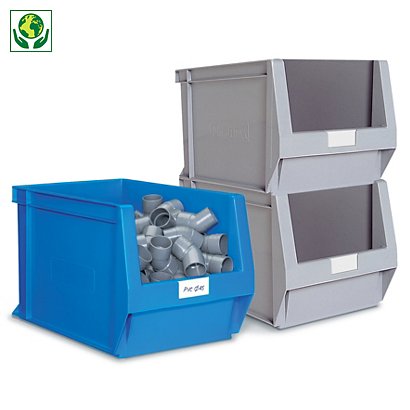
Large-volume plastic spout bins, to withstand all common acids and solvents. They are stackable and have a wide front opening for easy access to products.
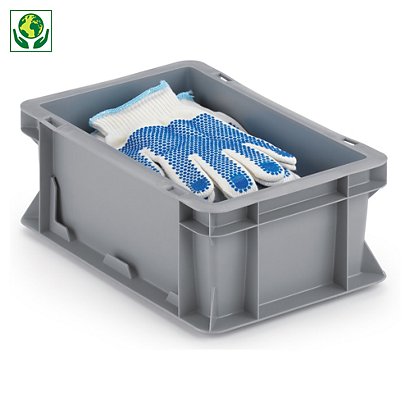
European standard stackable bins with closed handles, to withstand oils, greases, chemicals and temperature variations. They can be palletised and offer high stacking stability up to 200kg.
Storage crates
The crates can be stacked to improve space organisation.
They come in a variety of formats, including :
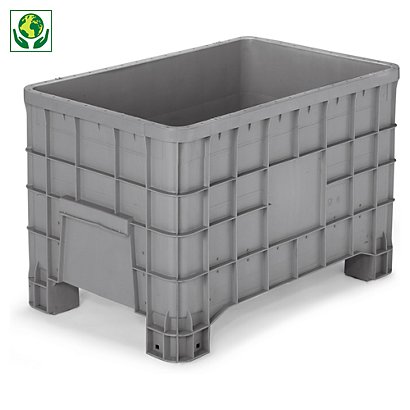
The plastic pallet box, stackable by 4, can hold up to 510 kg. They are fitted with handles and can be used with a pallet truck or forklift.

The folding pallet box, with the same properties as the classic box.
Handling equipment
This equipment is essential to facilitate the movement of goods, while ensuring the safety of employees.
Here are the machines we recommend:
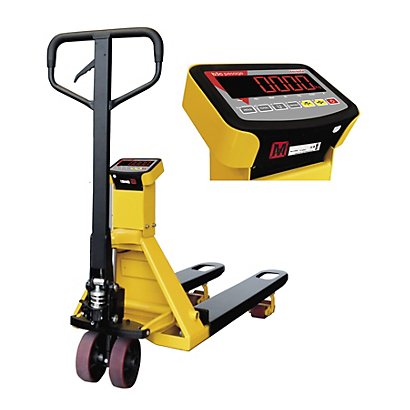
Manual or electric pallet trucks for moving pallets.
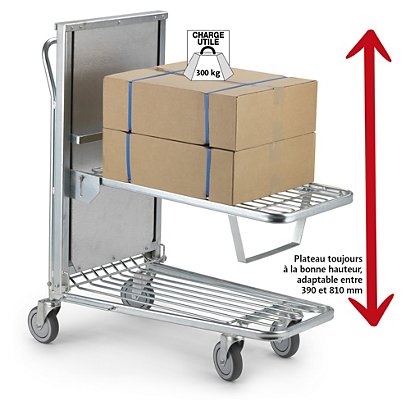
Trolleys, for moving heavy loads at the right height.

Rolls, for moving goods in complete safety.
Safety equipment
This equipment helps to ensure the safety of warehouse staff and reduce accidents.
Mandatory equipment includes :
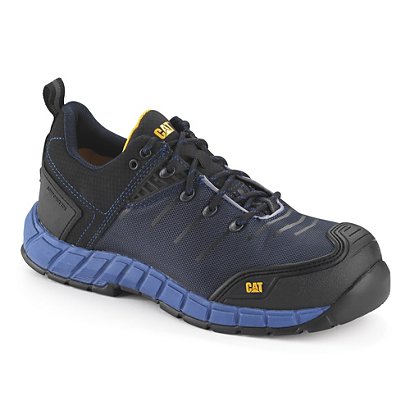
Safety footwearadapted to current standards.
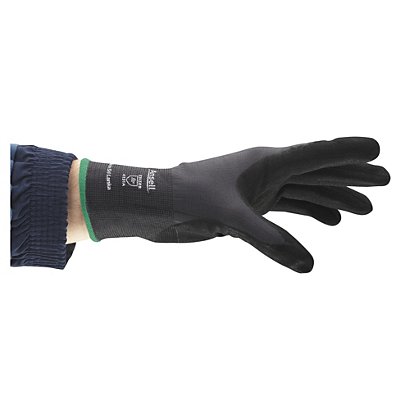
Safety gloveswith protection adapted to your needs (thermal, cut protection, dexterity, etc.).
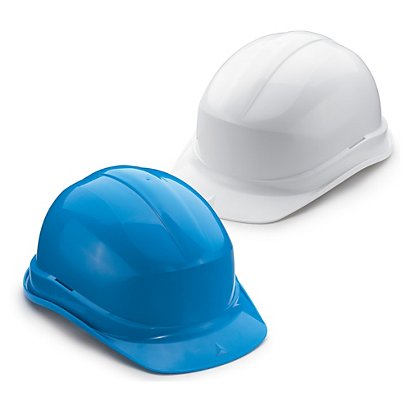
Safety helmetsfor protection against falling objects.
- Safety shoesadapted to current standards.
- Safety gloveswith protection adapted to your needs (thermal, cut protection, dexterity, etc.).
- Safety helmetsfor protection against falling objects.
As we saw earlier, picking is a crucial stage in warehouse management:
Discover our selection of essential equipment for B2C picking!
Discover our selection of essential equipment for B2B picking!
You now have a good overview of the main software, tools and hardware for stock management. Want to find out more? Discover the essential tools for stock management!
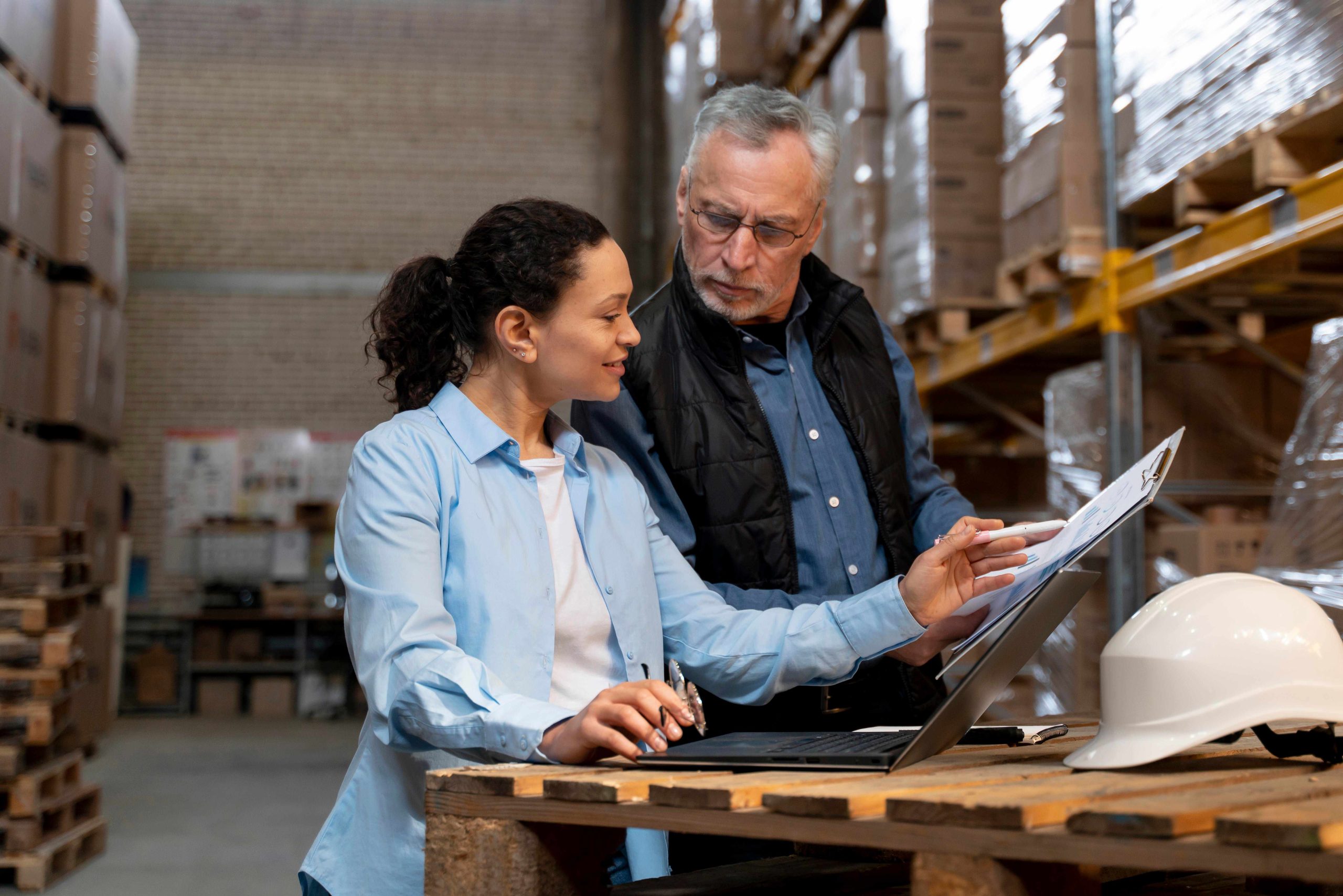
10 tips for optimising your stock management
Essential software for stock management
The stock management table
Companies that don’t have specific business software most often use Excel spreadsheets for their stock management.
However, Excel and its alternatives quickly reach their limits. It lacks automation, which implies a need for very detailed monitoring and regular manual updates.
The Warehouse Management System (WMS)
When the volumes stored are higher, it becomes necessary to equip yourself with software dedicated to this type of operation.
WMS offer a number of advantages, including
- improved productivity
- reduced stock levels
- analysis and forecasting of consumption
- optimisation of storage space
- reduced risk of order errors
Enterprise Resource Planning (ERP)
This type of software complements the WMS, making it easier to monitor stocks and inventories in real time, with a number of advantages:
- a global view and better control of stocks
- optimised flows
- automated replenishment
- analysis of consumption and behaviour
Advanced Planning System (APS)
This tool is designed to facilitate planning, from generation to transmission and distribution. In particular, it enables :
- better organisation
- process optimisation
- improved profitability
The essential tools for stock management
The barcode
In addition to software, it is advisable to implement physical solutions to facilitate stock management.
The barcode equips goods with a unique identification that can include a variety of data: dimensions, weight, storage characteristics, supplier name, quantity in stock, etc.
RFID technology
RFID (Radio Frequency Identification) is a wireless identification and data-sharing technology.
Each item is given a unique serial number and information. When coupled with warehouse management software, it boosts performance tenfold, with improved stock visibility and automated recording of receipts and deliveries.
Picking
Picking refers to the stage during which the picker retrieves the items in an order from the warehouse, putting them together to prepare the parcel.
This is a crucial stage in the supply chain and stock management. Optimising it will save you a lot of time and money in your day-to-day activities.
Find out how to optimise picking in your warehouse!
The picking list
The picking list, or picklist, is a tool that helps to reduce order picking errors. Its role is to explain to pickers which goods to pick for which orders.
It should contain the following information as a priority:
- The order number
- The area where the product is to be picked up
- The product code
- Product name and description
- Quantity to be picked up
- Customer information
Discover our guide to creating efficient picking lists for your warehouse!
Voice picking
Voice picking is order picking by voice. In practical terms, the picker is equipped with a headset and a microphone and is given the picking tasks, the areas where the goods are to be picked, the quantities to be picked, the place where the goods are to be deposited, etc.
However, there is some debate about this automated picking process. It’s important to find out all about the advantages and disadvantages so that you can make the best decision for your particular situation.
Find out all you need to know about voice picking!
Essential stock management equipment
Shelving
Racking allows warehouses to be laid out in a way that optimises stock placement.
There are different types of shelving, such as :
![]() |
Epoxy steel shelving, for lighter loads such as archives or files. |
![]() |
Galvanised steel shelving, for loads between 170 and 200 kg per shelf. |
![]() |
Galvanised steel shelving with chipboard top, for loads of up to 580 kg per shelf. |
Choosing the right shelving for your warehouse can sometimes be a headache. Check out our guide to choosing the right shelving!
Bins and totes
Bins can be used to organise shelving, particularly for storing bulk goods.
They come in different formats, such as :
![]() |
Spout trays made from polypropylene honeycomb to withstand water, grease, chemicals, impact, bending, tearing and temperature variations. |
![]() |
Large-volume plastic spout bins, to withstand all common acids and solvents. They are stackable and have a wide front opening for easy access to products. |
![]() |
European standard stackable bins with closed handles, to withstand oils, greases, chemicals and temperature variations. They can be palletised and offer high stacking stability up to 200kg. |
Storage crates
The crates can be stacked to improve space organisation.
They come in a variety of formats, including :
![]() |
The plastic pallet box, stackable by 4, can hold up to 510 kg. They are fitted with handles and can be used with a pallet truck or forklift. |
![]() |
The folding pallet box, with the same properties as the classic box. |
Handling equipment
This equipment is essential to facilitate the movement of goods, while ensuring the safety of employees.
Here are the machines we recommend:
![]() |
Manual or electric pallet trucks for moving pallets. |
![]() |
Trolleys, for moving heavy loads at the right height. |
![]() |
Rolls, for moving goods in complete safety. |
Safety equipment
This equipment helps to ensure the safety of warehouse staff and reduce accidents.
Mandatory equipment includes :
![]() |
Safety footwearadapted to current standards. |
![]() |
Safety gloveswith protection adapted to your needs (thermal, cut protection, dexterity, etc.). |
![]() |
Safety helmetsfor protection against falling objects. |
- Safety shoesadapted to current standards.
- Safety gloveswith protection adapted to your needs (thermal, cut protection, dexterity, etc.).
- Safety helmetsfor protection against falling objects.
As we saw earlier, picking is a crucial stage in warehouse management:
Discover our selection of essential equipment for B2C picking!
Discover our selection of essential equipment for B2B picking!
You now have a good overview of the main software, tools and hardware for stock management. Want to find out more? Discover the essential tools for stock management!
10 tips for optimising your stock management
#1 – Use an automated stock management system
Reduce the risk of human error and speed up your staff’s daily tasks by equipping yourself with software that will automate low-value tasks. Most also offer real-time monitoring of stock levels, as well as order and delivery management.
#2 – Define your minimum and maximum stock levels
Define the ideal stock volume thresholds for each item. The ideal range should enable you to avoid production shortages, while limiting the risk of overstocking. Remember to regularly adjust the thresholds according to the context of your market (variations in orders, shortages, seasonality, etc.).
#3 – Reduce dead stock
Track down and eliminate those stocks of obsolete or out-of-date goods that are taking up storage space unnecessarily. This frees up space for other items and avoids additional costs.
#4 – Automate replenishment
Set up systems to automatically launch alerts when stock thresholds are exceeded. This way you can anticipate orders and even automate them for even greater efficiency.
#5 – Define a procedure adapted to goods at risk
Set up an effective stock rotation system for your perishable products or those at risk of obsolescence. In this way, you can avoid generating new dead stock, while limiting the losses and unnecessary costs associated with it.
#6 – Carry out regular stock audits
Schedule physical audits to compare actual inventories with the data in your systems. If there are any discrepancies, identify the causes and make the necessary corrections.
#7 – Build a network of trusted suppliers
Build solid relationships with your most important suppliers. This is the best way to ensure you get reliable delivery times. Over time, it will also be much easier to negotiate better prices or conditions.
#8 – Segment your stocks
Classify your stocks of goods according to their importance (value, shelf life, space occupied, etc.). This will enable you to prioritise your resources on those that represent the greatest challenges for your business.
Do you manage very specific stocks of goods? Discover our dedicated guides for storing and shipping your vinyl or your comics or mangas!
#9 – Optimise warehousing
Organise your space to maximise the efficiency and speed of order preparation. Certain tools, such as WMS, can help you to identify the best storage locations based on a number of parameters, such as the frequency of incoming and outgoing goods.
Discover our top tips for organising your warehouse!
#10 – Analyse your data
Gather data from your various systems and tools to identify trends. You can then deduce the best levers for improvement to optimise your overall stock management.
Now you know everything you need to know about stock management! If you want to find out more, don’t hesitate to consult the dedicated resources we’ve linked to in certain sections.
And to find out more about our products dedicated to this subject, visit our website!