The logistics manager is the mainstay of the dispatch area: he or she orchestrates the removal of parcels from stock and the transport of goods, ensuring the quality of shipments and optimising costs. However, once the parcels are ready for dispatch and have left his or her control area, the logistics manager often has to deal with external problems: theft, breakage, etc
Here are 5 logistical problems that logistics professionals frequently encounter… and our advice for avoiding them!
This article was updated in October 2020.
Logistics problem number 1: lack of storage space
If the warehouse where you store your goods is too small to accommodate all your packaging supplies, you need to optimise the workspace to improve flow management.
Reduce packaging space with space-saving products (e.g. bubble wrap is small and can be easily replenished within 24-48 hours).
Rather than stocking 3 weeks’ worth of materials, opt for 3 days’ worth ofstorage that is replenished twice a week, on fixed days of supply and with the ability to adjust as needed. Your stock management will thank you for it!
Work space should not be neglected ingenious solutions can be adopted in your warehouses:
- The compact packing station: it includes several mobile shelves, space for a work screen as well as overhead storage.
- The ergonomic workstation: adaptable in width and height, with the possibility of adding tables and accessories, it allows for great modularity and space saving with its shelves, racks and beaker trays for example.
- The motorised ergonomic workstation, which can be adjusted in height by means of motors that raise the work surface, for optimum ergonomics at your order picking station.
Logistical problem no. 2: the cost of transport
The cost of transport is one of the key issues for transport and logistics managers, whose job includes optimising costs.
Here are some solutions to optimise your transport budget:
- Reduce the weight of the packaging by reducing the weight of the cardboard and the cushioning, for example from 50 g to 10 g.
- Avoid overloading the cushioning with a cardboard box of the right volume.
Do your cost-benefit calculations: cardboard A + cushioning B or custom-made cardboard? Which solution will have more impact on your overall logistics budget?
Another alternative is variable height boxes, such as the Variabox from RAJA, which can be adapted to the height of the product thanks to grooves every 2.5 cm; you have 5 different heights for the same box.
These boxes allow you to save on cushioning materials as well as on storage space, by reducing the number of references to be managed.
Also think about reducing the size of your shipments for small goods: if you can fit them into a letterbox, take a special extra-flat box and avoid the cost of a logistics provider for your transport.
In the end, it’s all about the right box in the right size that will optimise transport costs
Logistical problem number 3: breakage or spoilage
At the top of the podium, broken goods or damaged packages are a major problem for the seller and the carrier.
In 23% of cases, a package with damaged packaging will have a negative impact on customer perception(source: Packaging Insight x Prégis, 2016)
And to drive up the bill, there is more than a 70% chance that the customer will not order from you again.
To avoid breakage throughout your supply chain, you can use :
- A “Fragile” label;
- Fragile” tape.
To avoid damaged packages, make sure you :
- Use strong cartons;
- Choose cartons that are the right size for the product.
- Opt for appropriate protective cushioning
Simple practices, to be incorporated into your logistics practices from now on, to have (more) peace of mind when delivering your goods.
Logistics problem n° 4: theft or loss
Number 2 on the podium of problems encountered by logistics managers, theft and loss are the scourges of vendors and transporters.
To avoid theft, secure your parcels as best you can with :
- Crates with self-locking bottoms.
- The right adhesive: choose the one that will cling best to the box. There are several types of adhesive, more or less strong (gummed tape, reinforced adhesive, etc.).
- A little more adhesive on the edges of the box.
- Strapping the package: this makes it very difficult to open the box but is not suitable for shipment via the Post Office (the strapping can get caught in the conveyor system).
- The opaque security pouch with an adhesive showing “void fraud” in case of infringement is suitable for certain goods.
- Black stretch film for your pallet shipments
To avoid loss and ensure the traceability of your parcels, take care of your labels and make sure they are legible. Losses are sometimes only temporary but lead to many complications and unnecessary return trips.
Logistical problem No. 5: clearing customs
Going through customs is a complicated stage for carriers, as packages can quickly be blocked or refused. To avoid this, take a few precautions:
- Standardised packaging for certain countries or regions of the world.
- Regulatory packaging for sensitive products (e.g. batteries should be sent in special packages).
- Clear labelling for overseas shipments, with an address according to the standards of the destination country.
- A standardised pallet according to ISPM15.
- A self-adhesive document pocket with all the information and certificates needed for customs clearance.
By taking the necessary steps to avoid these 5 recurring logistical problems, you will ensure optimum management of the logistics chain.
The three key points to remember
- With the right packaging (a box whose dimensions are adapted to the products) you will avoid breakage, theft, and optimise your transport costs.
- Organising the logistics of the shipment also involves optimising the workspace: as a logistician, you must ensure that practical and ergonomic logistical solutions are in place to do this.
- Problems during shipments are rarely the fault of the sellers, but they are the ones who most often pay the price: it is therefore better not to take any risks and to take care of your packaging.
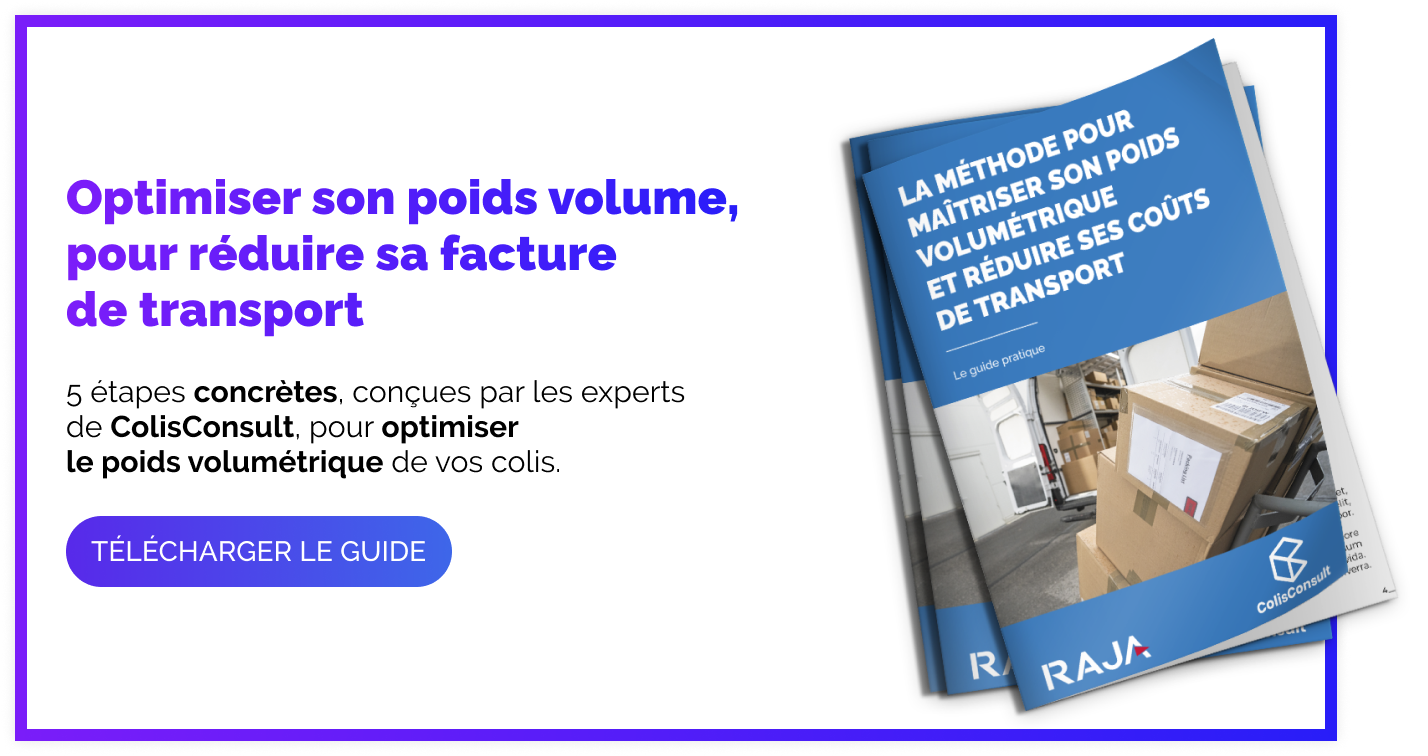