The time spent on order preparation in the warehouse is a key element in the calculation of the overall logistics cost, and all companies are looking to optimise it: this is why you need to choose your preparation method carefully, depending on your shipping thresholds and your activity.
The order picking process consists of organising the key stages of a parcel in the warehouse, namely
- Picking: the operator is responsible for picking the items needed to make up the orders.
- Sorting: once the articles have been picked, they are distributed among the respective orders.
- Packing: the items are packed once they have been grouped together.
By the end of this article, you will have discovered 3 order picking methodologies to improve your transport and logistics strategy, while limiting errors in your deliveries.
This article was updated in September 2020.
What is picking in order preparation?
When the warehouse receives large quantities of goods, they must first be stored on the shelves and then delivered daily to a “picking” area.
This area allows for the storage of :
- Small quantities of products;
- The most popular“best-sellers “;
- Products that are accessible by man or machine for operators and order pickers.
This is where the products are picked up and taken to the packaging area and then to the area dedicated to their dispatch.
Picking, like the rest of your warehouse, can have its logistics optimised by various methods.
Note: In a shop, this picking process is called “warehousing”, but note that this article is dedicated to picking methods in a warehouse supply chain? |
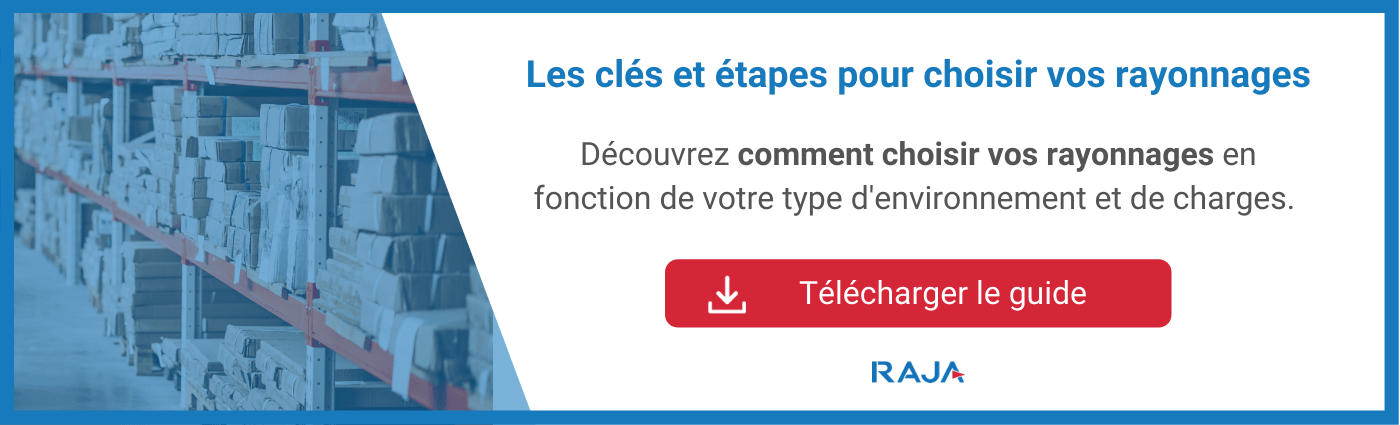
The “Pick and pack” method
How does the pick and pack method of order picking work?
- The order picker picks up the required goods indicated on the order form, takes them to the packing area and then returns to pick up the products of another order. This method is obviously not the fastest and is suitable for very low shipment thresholds during the same day, such as for small e-commerce activities.
- The best method of “Pick and pack”: when the order picker picks up all the items from several orders at the same time and distributes them into organised bins on a picker trolley, before packing them.
The “Put to light” method
How does the “Put to light” method work?
Literally meaning “put to light”, this method works with trolleys equipped with light screens to indicate to the operator where to look for and put down the necessary products.
This allows for efficient picking from bulk stock.
The operator then drives his trolley to the bins where the orders are distributed: his “Put to light” displays will light up in front of each location to show him in which bin or box he should place his item.
This method has two main advantages:
- This guidance system allows the logistics operator to prepare and group several orders at the same time.
- It allows the order picker to minimise the risk of errors or omissions, thanks to optimal traceability of his picking activity.
The “Pick by light” method or global picking
This picking method also works with light signals and is very useful when the order threshold is high, to minimise the risk of errors.
The operator can easily recognise where each product is to be picked and how many items are to be picked.
Once the products have been picked, the operator triggers a customer order release, received directly from the central stock management terminal.
This allows for continuous replenishment from the storage area to the picking area, thus avoiding breaks in the process.
The operator will then scan each item to be able to proceed with the handling, and deposit it in the place indicated to him by indicator lights in the aisles.
Thanks to the light signals, the operator knows at a glance the current status of the orders to be prepared, without having to refer to the order forms:
- Green = complete ;
- Green = complete; Red = incomplete.
This method also has many advantages:
- It allows many orders to be prepared at the same time
- It increases the productivity of the entire order picking logistics chain.
- It reduces the risk of forgetting or making mistakes in the picking process thanks to effective light signalling.
- It works in harmony with the central warehouse management system (WMS or ERP), thus reducing the time spent by your employees in managing stock orders.
As a result, employee productivity is increased.
Put to light” and “Pick by light” systems, however, require efficient computerisation of the warehouse and entail high equipment costs.
In spite of this, your logistics warehouse quickly gains in productivity: the number of picking errors is considerably reduced, logistics operators can prepare more orders at the same time, and the management system is streamlined to avoid stock shortages.
To go further Have you heard of Voice Picking? This method of order picking can be very effective, but it is changing the order picker’s job permanently.Find out the pros and cons of this method in our dedicated articlethis is a method of order picking that uses technology to prepare orders more quickly.
|
Conclusion: what you need to know about these picking methods
- Pick and pack” is a traditional method that can be used in logistics warehouses that do not have a high daily order flow.
- In order to avoid human errors in order picking, such as forgetting or confusing products, automation and the “Put to light” and “Pick by light” systems are particularly recommended.
- The indicator light system stands out because it simplifies the recognition of products and locations. However, this requires a certain amount of equipment in your warehouse. But productivity and customer satisfaction are multiplied.
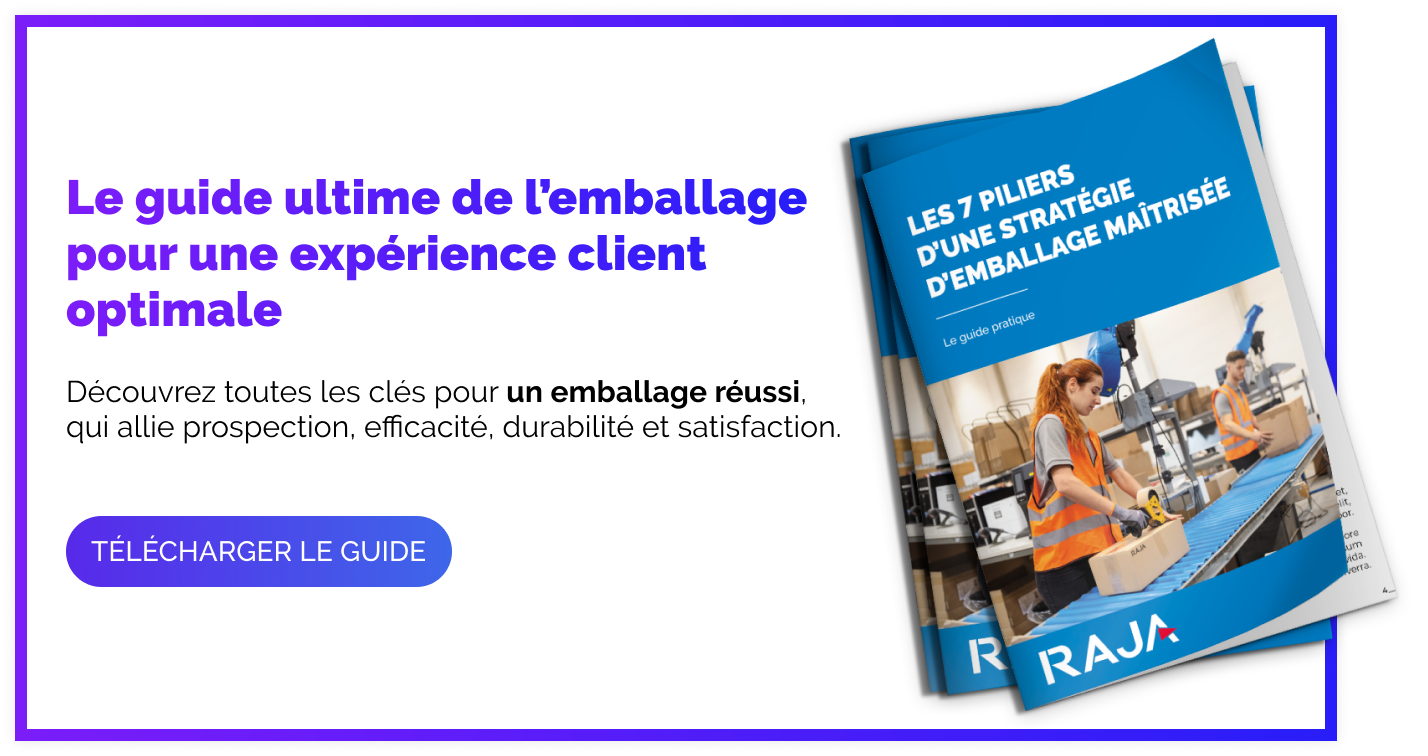