0201, 0300, 0340 – does it mean anything to you? Or is it just gibberish?
FEFCO codes are designed to bring order and structure to the vast and sometimes rather confusing market of boxes and cartons. But how do these FEFCO codes work? We’d like to give a relatively simple explanation in this blog post.
1. What does FEFCO mean?
The acronym FEFCO stands for Fédération Européenne des Fabricants de Carton Ondulé – an association of European corrugated cardboard manufacturers. This non-profit organisation is based in Brussels and deals with all issues relevant to the production of cardboard packaging. One of their many achievements is the development and updating of the FEFCO codes. This international coding gives the cardboard boxes a common language – in other words, an international understanding of the type designation of cardboard boxes. How it works:
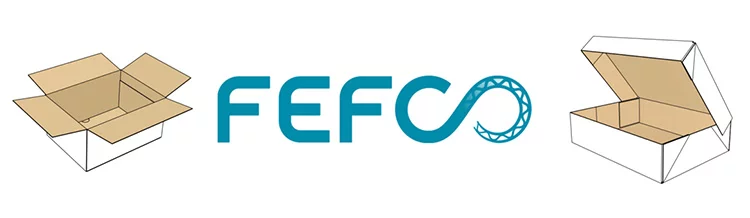
2. What are the FEFCO codes?
As diverse as cardboard can be, so are the design options for cardboard boxes and packaging. Anyone who has ever put together a box will have noticed how many perforations, folds and glues can be different. While all this has a practical reason, it also complicates communication between users, retailers and manufacturers. That’s why FEFCO decided in the 1960s to standardise the names of cardboard boxes using a simple number code. You can now find these FEFCO codes all over the world. Thanks to the FEFCO code, everyone speaks the same ‘language’ and misunderstandings about size, shape or design are avoided thanks to the codes.
FEFCO has also standardised the technical drawings for folding boxes. This makes it clear at a glance where to fold inwards and where to fold outwards, where to cut, scratch or glue – and always with a clear goal in mind: “FEFCO wants to replace cumbersome definitions of corrugated boxes and packaging with simple, internationally recognised symbols that are universally understood, regardless of language or other barriers.”
3. How is a FEFCO Code composed
The FEFCO code allows all solid board or corrugated boxes to be categorised into different basic types. The FEFCO code number consists of four digits, e.g. 0201 is the code for a classic folding box made of corrugated cardboard (one of the most common variants in Denmark). The code contains information not only about the shape, but also about the way you close the box. For example, box 0712 is one with flaps, while variant 0713 is one with a lid.
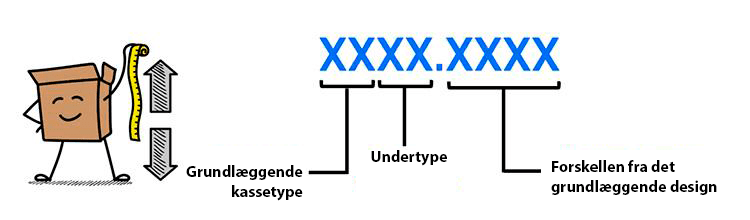
The basic four-digit code can be supplemented with a maximum of four extra digits. These extra numbers then indicate a different version of the basic design. For example, the code 0229.1 was added in 2022. The last ‘1’ indicates a new variant of the basic design 0229.
The two digits at the beginning of the code always indicate the basic type of box. The FEFCO catalogue is divided into the following nine basic types:
Basic type | Characteristics |
01 – Rolls and sheets![]() | – Made from long rolls of corrugated cardboard. – Starting shape for all other shapes in the FEFCO catalogue. – Example: folded cardboard or interlayer. |
02 – Folding boxes![]() | – Made from a single piece of corrugated cardboard. – The ends are fixed together with glue or staples. – Can be closed by flaps. – Supplied flat to save storage space. – Example: folding box made from double corrugated cardboard. |
03 – Boxes with lids![]() | – Consists of at least two components. – Both parts can be set up separately and must be placed on top of each other after filling the box. – Example: expandable box with lid. |
04 – Postal boxes![]() | – Made in one piece. – Parts fit together before closing via slits or flaps on the sides, so no gluing or stapling is necessary. – Example: brown postal box. |
05 – Cover / Wrap![]() | – Consists of several sleeves that slide into each other (possibly from opposite directions). – Is glued or stapled during production. |
06 – Dimensionally stable boxes![]() | – Consists of several separate pieces that have been joined together during the production process. – The rigid construction ensures a particularly high level of stability. |
07 – Boxes with automatic bottom ![]() | . – Manufactured in one piece. – Set up in seconds: ideal for quick assembly of parcels. – Example: boxes with automatic bottom. |
08 – Retail and Ecommerce![]() | – Offers typical formats and styles used, for example, for display in shops or for storage and shipping via online shops. – Example: cardboard picking box. |
09 – Interior![]() | – Rooms, floors and partitions. – Serves to protect the packaged goods: the contents cannot slip or break. – Example: bottle packaging with vertical dividers. |
4. What are the standardised packaging dimensions?
Box dimensions always consist of three dimensions: length, width and height. With an almost infinite variety of box sizes, it is not always clear which number indicates the length, width or height. The good news is that this is standardised in a fixed order – and the order is: L x W x H.
Length (L) = the longest side of the open box.
Width (W) = the shortest side of the open box.
Height (H) = the inside edge from the bottom of the box up to the opening.
By default, I mainly choose the inner size of a box. You can read more about this below. The unit of measurement for the dimensions is also consistent. This is given in millimetres. This way, errors in measurements can be avoided as much as possible. However, in exceptional cases, box dimensions may be shown in inches (= 2.54 cm) or cm (= 0.393701 inches).
5. Inside or outside dimensions of a box?
What is the best way to indicate the dimensions of a cardboard box? Should you give the internal or external dimensions of the box?
The difference between these two sizes can vary considerably, depending on the quality and thickness of the cardboard (single corrugated, double corrugated or triple corrugated). Below we have provided a few useful guidelines:
- The inside size is the standard term for box dimensions. This allows you to perfectly determine the box size based on the items to be packed in the box. It is important to choose the box a few millimetres larger than the dimensions of the items to be packed. This is partly because there may be production deviations in the cardboard boxes (for example in the thickness of the cardboard material) and partly because it makes it easier to pack and later remove the goods at the customer’s premises. Particularly sensitive products may also require packaging fillers to protect the contents, so remember to factor this into the size.
- The external size of a box is also important to be able to correctly assess the available space in your warehouse or in a lorry. If you are stacking boxes on a pallet, this is obviously the measurement you need to pay attention to. To calculate the outer size, measure the dimensions of the sides of the closed box and add a material tolerance of 5 mm.
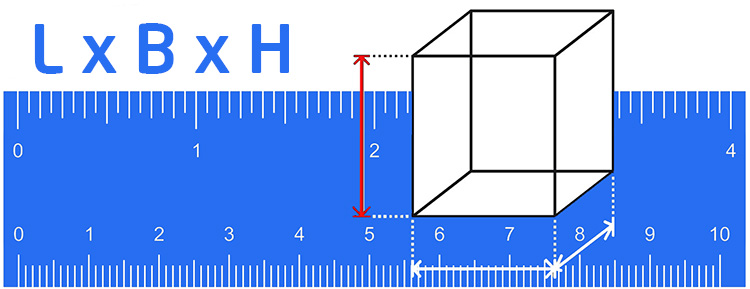
6. How to create a customised box?
Do you usually pack only 1 specific product? Then a customised box can be the perfect solution and allow you to save on packaging material. The better the box fits around your product, the less padding is needed inside. The small extra cost of a customised box will therefore be recouped twice over on your other packaging costs. It all starts with the development. As soon as this design is approved by the customer, we order the necessary die-cutting tools for production and – if printing is required – the corresponding clichés must be ordered.
During production, the individual layers of corrugated cardboard are brought together and glued, then die-cut and printed. There are several options for printing the finished cardboard, depending on what is required. Offset printing is particularly suitable for gift boxes or displays. Here, the design is printed on a carrier foil and then applied to the corrugated cardboard.
In screen printing, the relevant print is applied directly to the surface to be designed using templates. Due to the slightly longer production time, this method is particularly recommended for smaller quantities. Flexo printing is the third option and the most commonly used printing method for corrugated products. For example, it is often used to apply logos directly onto the packaging.
We always use inside measurements on our cardboard boxes in RAJA. Below you can enter your measurements and find the cardboard boxes closest to your enquiry.
[su_boxselector]