Since its invention in 1882, corrugated board has been a popular and, above all, durable filling material for protecting products from impacts and shocks.
But why is cardboard so stable?
Firstly – of course it’s because of its shape. Its corrugations, or waves, which spread the point pressure over a large area, make it far more resistant to mechanical pressure and punctures.
The second influencing factor is the quality of the bonding of the (at least) three layers of cardboard. The better the adhesive is absorbed into the paper, the more stable the paperboard is. A sign of quality is, for example, the tear test: the more fibre residue that remains on the two torn layers, the better*.
A third distinguishing feature is, among other things, the number of processed wool layers and cardboard separating layers: common for three-layer corrugated boxes (with one layer of wool), five-layer boxes (with two layers of wool) and seven-layer boxes (with three layers of wool). The layers of wool are always separated by a layer of smooth paper. The three-ply box is therefore a seven-ply box and is therefore one of the strongest paper materials. The seven-layer boxes have a load capacity of several hundred kilograms and are most often used for the transport and storage of heavy goods in the construction or automotive, chemical and electrical industries and for export.
The strength of the cardboard is determined during production by the choice of raw material. The proportion of old paper plays a less important role. A higher proportion of kraft paper, i.e. new fresh fibres, leads to higher strength, greater moisture resistance and thus greater stability of the corrugated board. .
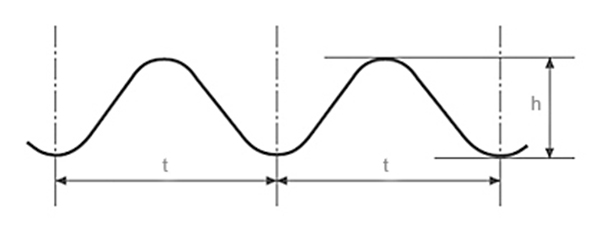
In addition, the ratio of the wave height (h) to its length (t) from valley to valley is important for shock absorption. Depending on this height, the corrugations are divided into type A (also called coarse corrugation) through medium C and fine B, up to corrugation E (also called microcurrent corrugation). The smaller the corrugation, the lower the possibility of safe stacking (thus reducing the resistance to static-mechanical loads) and also the damping properties. The contents of the paper box must therefore be all the more resistant, i.e. they must contribute to the pressure equalization from the outside, e.g. the material of the inserted goods is more resistant, or it is wrapped with bubble wrap or fixed with floppy filler material, etc. Small corrugations can thus be used for flat and stable items such as magazines or books. Large corrugations should be used for delicate goods. On the other hand, however, the smaller the ripple, the easier and better the printing.
* Source: http://www.wellpappe-wissen.de/wissen/wellpappe/bauprinzip/verklebung.html?PHPSESSID=29df69d32f8adede7be340e5fab2a619