Order errors in the warehouse are not uncommon and can be caused by a number of factors: a non-optimised storage method, a poor distribution of tasks between operators, poor signage in the warehouse, etc
However, there is one logistics tool that can help you reduce the rate of picking errors: the picking list, which tells your pickers which products to pick for which orders.
In this article, we give you our expert advice on how to create truly effective picking lists that will reduce human error and increase productivity in your warehouse.
- What are the characteristics of an efficient picking list?
- What format should your picklist take?
- What information should appear on a logistics picklist?
- A picklist model to inspire you
What are the characteristics of an effective picking list?
It is well known that as a stock grows, the number of items increases and the risk of picking errors increases, which is why it is crucial to design your picklists and make them as clear as possible for your operators
The ideal picking list should :
- Contain only what is useful to the operator, so that the picker can read the list more efficiently with just the right amount of information.
- A picking list shouldallow the picker to track his activity and easily trace the source of any errors.
- Be organised according to your activity. If you often prepare orders containing a large volume of the same references (as may be the case in B2B, for example), your picklists should emphasise the quantity of products to be picked. If, on the other hand, you prepare orders that are very different from one another, the emphasis should be on the differences in references between the products to be grouped.
Think of what the order summary page looks like on an e-commerce site, before payment, where the different products ordered are listed together. Here you can see what an ideal picklist looks like: a clear document where each of the different elements is easily readable.
What format for your picklist?
A picklist can take two different formats:
- The printed picklist: Picking lists are often printed on loose sheets, especially in e-commerce warehouses with few products in stock.
- Digital picklists. Where operators have a tablet or other handheld device, picklists can be broadcast in real time. These have the advantage of being more detailed, including photos of products to avoid mix-ups.
If your warehouse is equipped with a WMS (Warehouse Management System), your picklists can be automatically generated by the software.
However, whatever the format of your picking lists, you need to ensure that they are easy to understand at a glance. The more complex the format of your picklist, the more likely you are to make frequent ordering errors.
Voice picking: THE solution to reduce order errors? Whether you are for or against voice picking, there is a lot of talk about it, but is it an additional productivity booster or a dehumanised method that increases psycho-social risks for employees? Because it is worth considering the question before considering implementing it, we recommend that you read our article: “For or against voice picking?” |
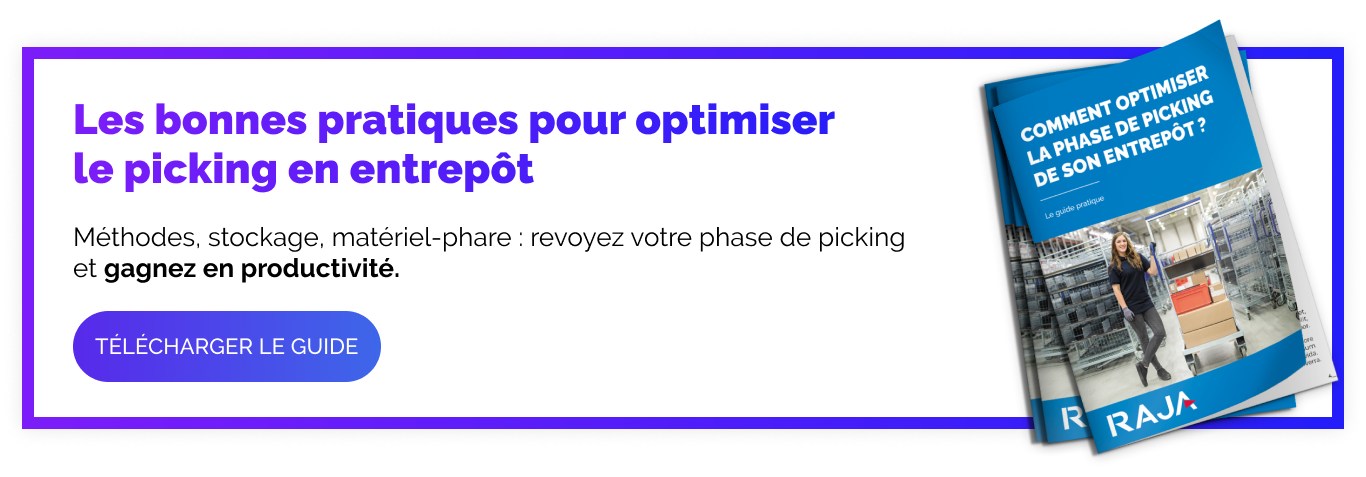
What information should appear on a logistics picking list?
While the format of the picklist is important in improving your picking methods, the most important thing is the information that is presented to the operators. Which information should be selected to create truly optimised picking lists?
The order number
The order number is essential to indicate on your picking lists. Not only does it allow you to differentiate one order from another during the picking phase, but it is also crucial if a problem occurs on the picking line
The order number is a key element in the picklist, as it allows you to easily trace products returned by customers, or products that have never been received, from the picklist.
The area where to pick up the product
One of the first pieces of information your operator will need is of course where in the warehouse to pick the product. Whether you have determined several zones in your warehouse, or have numbered your racks, indicate the location as precisely as possible on your picking list.
Of course, the easier it is to locate the product, the more efficient your picking chain will be, which is why optimising your picking process necessarily involves optimising your storage method, as well as well organised signage in the warehouse.
The stock keeping unit / product code
Any well-organised warehouse will have a unique code for each product: this code is called the stock keeping unit (SKU). If you sell shoes, for example, each size will have a specific SKU.
The SKU not only helps you to keep track of each item, but also reduces the risk of errors during the picking phase. Well marked on the racks or bins, as well as on the picklist, the code of your product cannot be confused with another, and makes the picking of your pickers more efficient.
Product name and description
In addition to the SKU, an optimal logistic picklist includes a product description, which helps operators to visually locate the product in the warehouse. If possible, do not hesitate to add a representative picture of the product to your picking list.
The quantity to be picked
Your operators need to know, at a glance, how many of the same product they need to pick, so include a column on your picklist indicating the quantity to be picked.
This column must be well highlighted visually, so that it stands out well when reading, and avoid picking errors.
Information about the customer
Your pickers don’t need to know the identity or address of the customer who placed the order, but further down the picking line, the packers will
With this information, your picking lists become a relay between the different links in your preparation chain, which are passed from hand to hand, verifying the accuracy of the order until its final dispatch.
A picklist template to inspire you
To help you create your own optimised picklist, use this template:
Order number | Picking zone | SKU / product code | Product name | Qty to pick | Customer name and address |
#1 | |||||
#2 | |||||
… |
You now know what to include in your picking lists to optimise this crucial phase of the order picking chain
However, remember that an optimised picking process requires attention to other elements.
To really gain in productivity, make sure you :
- Take care of your storage method. There are various methods available: you need to choose the one that best suits your activity and your flows. To do this, consult our article “Which storage method for optimised logistical picking?
- Check that your products are correctly labelled in the warehouse. Labelling your racks, shelves and other picking bins is essential for your operators to maintain optimum productivity, by limiting the number of order errors.
- Choose the right equipment for your picking: to do this, consult our guide on the ideal equipment for BtoB picking, or the one on the equipment needed for BtoC picking.
- Have optimal picking tables that allow for efficient, error-free packing. To do this, see our article “How to choose your packing station or table”.
And for the final tip: always keep in mind the 5S approach, the basis of any efficiently managed warehouse. Originating in Japan, this method will enable you to optimise the time and working conditions of your teams, but also to plan the flows of your entire supply chain.
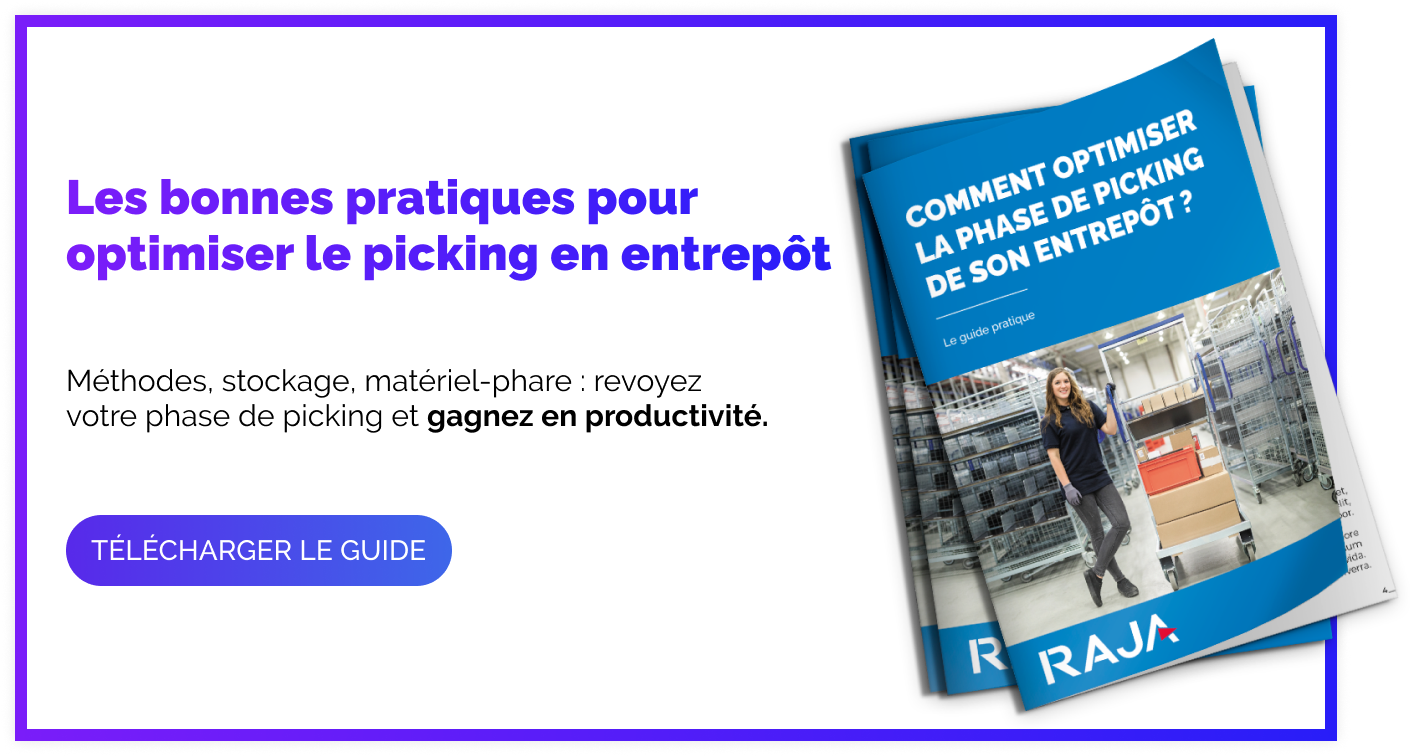