Order picking is a key point in the logistics of a warehouse, and is a key stage in delivering your customers on time.
Read on for our suggestions on how to improve the organisation of your flows and reduce errors.
This article was updated in December 2020.
What is order picking?
Order picking consists of grouping the items stored in the warehouse before they are sent to customers.
How does it work? Regardless of the method used, an order preparation follows the following steps in succession:
- Picking:this is the stage where the picker collects items from their storage location.
- Sorting: this is the stage where no mistakes are made! It consists of identifying and gathering the items corresponding to each unique order.
- Packing: once the products have been collected and sorted by order, they are packed for shipment.
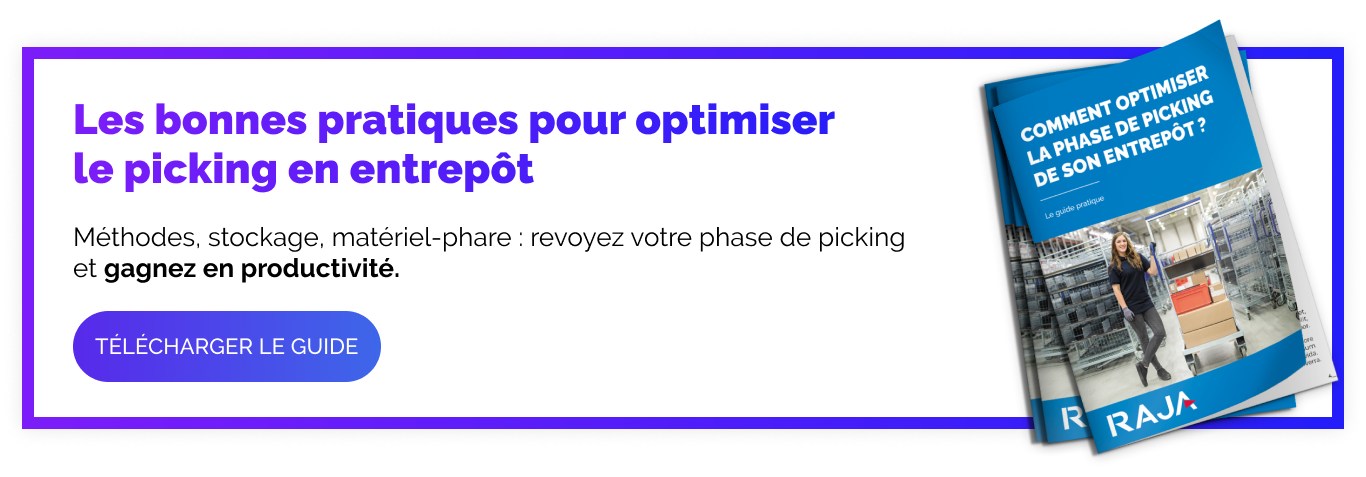
Essential information to provide to your order picker
To avoid human error in picking, you need to provide your picker/logistics operator with the right information to make their job easier, thus saving time, increasing productivity and improving accuracy.
Here is the essential information to know before picking the products:
- The picking addresses of the references to be prepared;
- The number of products to be picked, not forgetting to indicate the quantity per reference (a reference may be ordered several times in the same order);
- The collection areas where to deposit the pickedproducts.
This information, to be included on the order form, will enable the picker tooptimise his picking route, by order of picking of the articles, and thus avoid unnecessary backtracking.
Note: nowadays, the information needed to prepare an order is transmitted to the order pickers via paper documents or electronic terminals (portable or on-board trucks). The automation of these preparation orders makes it possible to limit potential errors.
Areas for improvement in order picking
To optimise your order picking and achieve a minimum error rate, you can consider these logistics improvements.
Reducing travel time
Far from being a detail, forgetting or misdirecting picking zones increases the order pickers’ travel time .
To save time on routes and prepare orders more efficiently, you can :
- Opt for an ABC type classification of references, by stocking the most ordered in terms of volume at the most accessible and closest locations, because often 80% of sales correspond to 20% of references.
- Respecting picking movements that do not force the picker to go to the same location many times.
Limit stock-outs
What could be worse than a break in the load of several products at the time of order preparation?
To avoid this , consider :
- Tracking goods movements with a central computerised stock management system;
- Replenish picking on a recurring basis with an automatic alert system.
This will eliminate unnecessary unloading from your picking method!
Ease of product picking
Certain picking methods can make your operators’ work much easier, such as the use of barcodes. How does this work?
- Using an on-board computer terminal, you simply scan the barcodes of the goods to ensure that you are in front of the right location and the right product reference.
- This system has the double advantage of limiting errors and monitoring the stock situation in the picking area in real time.
Optimise the accessibility of the articles
The picking area must be planned and organised in such a way that all products are accessible by hand, without the need for handling equipment such as forklifts.
- Do not store your products in racks 2 m high, as this will not only waste your handler’s time but also cause unnecessary risks (falling objects, etc.).
- Similarly, do not store products too deep in the shelves: they would then become difficult to access.
How to set up an intelligent storage system?
Also known as warehousing, proper storage of stocks ensures safety and good circulation of employees, but also optimises space. Here are some tips for storing your stocks:
- Organise your storage logically: avoid placing heavy objects high up to limit the risks associated with handling and to avoid damaging the balance of the shelving.
- Set upaisles that allow pickers to pass each other and/or pass each other to avoid traffic jams and accidents.
- Organise your shelves according to the nature of the products, their weight, etc.
As you can see, optimising your picking process is sometimes just a matter of organisation and logic. By preparing detailed customer order forms for the pickers, indicating the right picking routes and arranging your products so that they are accessible, you will gain in productivity and increase your daily dispatch rate.
Have you implemented any of these measures to improve picking speed? Please share your tips and advice in the comments below.
Three key points to remember:
- Order picking is a key stage in warehouse logistics, responding to two imperatives: do it quickly and do it well.
- In order to do well when going fast, you need to prepare the ground for your operators with clear and precise instructions to avoid mistakes.
- Think of simple but effective ways to improve, such as tracking stock to avoid stock-outs or marking out double lane aisles to avoid traffic jams.
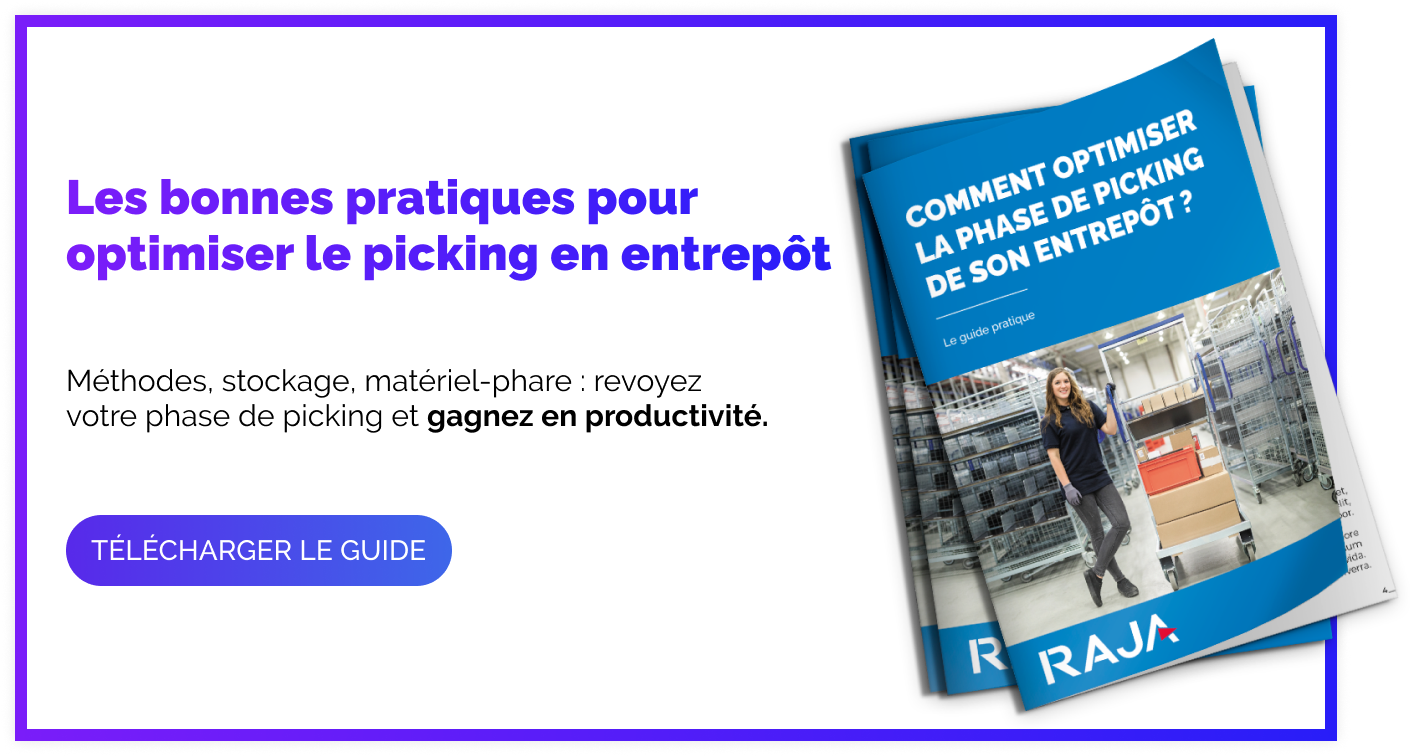