Order picking in a logistics warehouse can be a real challenge. At the heart of this daily challenge, which e-tailers know well, there is one key stage that makes the difference at the end of the packing chain: picking. Find out in this article what picking is, how to choose your method and the specificities of picking in an e-commerce warehouse.
- What is picking?
- What is the difwhat is the difference between picking in the warehouse and picking at the point of sale?
- What picking methods exist?
- How do large warehouses manage their picking?
- How can you adapt your picking method when you are starting out in e-commerce?
1. Qu’est-ce que le picking ?
En Anglais, le terme “picking” signifie littéralement “cueillette”. Il s’agit de l’une des étapes-clés de la préparation de commandes en logistique.
Le picking est le moment où l’opérateur va chercher les articles d’une commande, pour les rassembler en un même endroit. S’en suit l’étape de colisage, où l’opérateur prépare le colis qui sera expédié ensuite.
Comme toutes les étapes de préparation des colis, le picking logistique peut être optimisé. L’objectif d’un tel processus sera d’avoir à proximité de la zone de colisage les articles dont les opérateurs auront besoin, pour limiter au maximum leurs déplacements dans l’entrepôt. Par conséquent, le temps de préparation de commande sera réduit, la gestion des stocks optimale, et la manutention facilitée.
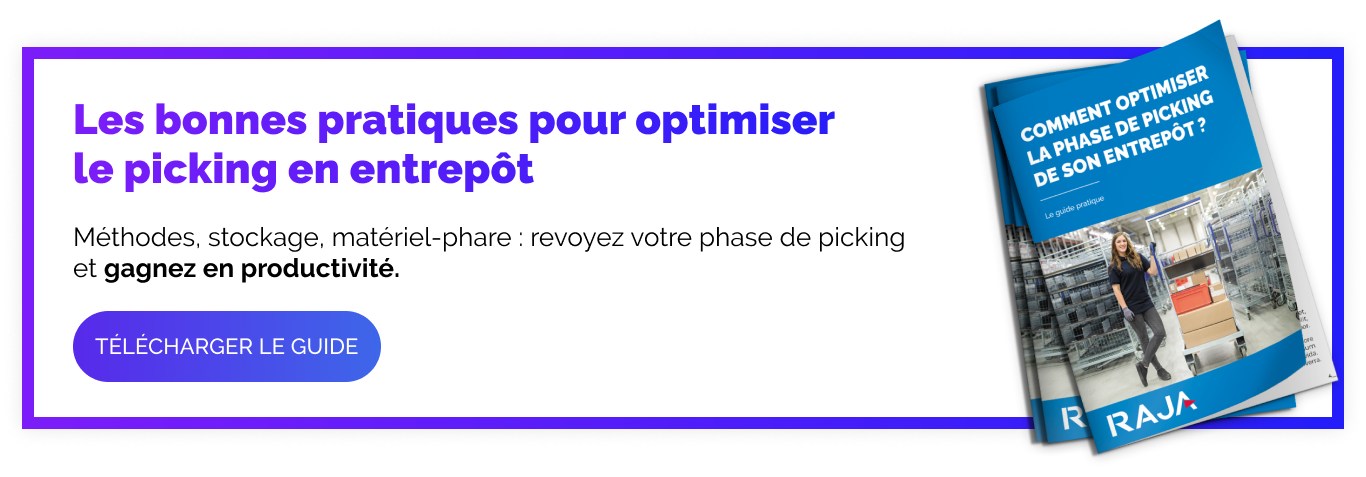
2. Quelle différence entre le picking en entrepôt et le picking en point de vente ?
Dans ce
- Warehouse picking consists of preparing orders, whether B2B or B2C, within the logistics warehouse. The orders are then sent to the point of delivery.
- Point-of-sale picking, also known as “in-store picking”, consists of preparing orders in the shop. Operators collect the items from the shelves or the store’s stock, and then make a home delivery or offer a drive-through service, where customers collect the goods in the shop.
the difference between these two types of picking is quite simple to understand
- On the one hand, warehouse picking is mainly done for e-tailers who do not have a point of sale where they can store their items, and on the other hand, after the warehouse picking phase, transporters will intervene in the delivery: the packaging of the package then becomes essential to avoid breakage.
- This is not the case for picking at the point of sale, where the shop is responsible for delivering directly to the customer, which makes packaging much simpler.
the difference between these two types of picking is quite simple to understand:
the storage of items in the warehouse is quite different from that in the shop. In the case of the former, we are faced with dynamic picking, which changes according to logistical issues, such as the seasonality of the goods, or the volume of items to be picked by the operators.
Doyou have these differences in mind? Let’s take a look at the different picking methods available to you.
3. What picking methods are there?
There are two main principles that govern picking in the store
- The “man to article” process: the order picker goes to the store to pick up the products;
- The “article to man” process: this is an automated picking process, where the article comes to the operator, thus limiting his movements.
depending on the principle that you wish and are able to put in place, different picking methods exist.
Man-to-man picking: the different methods
When the operator moves to pick the items in the order, he can proceed in several ways
- The “Pick and Pack” method will require the picker to pick the products needed for one or more orders, and take them to a packing area. Often the operator uses a printed order list.
- The “Put to Light” method equips operators with a trolley with light displays, which indicate where the required products are located and where to put them.
- The “Pick by Light” method also uses lights and messages. These are displayed at the storage location where the items are to be picked. The operator can then easily recognise where each item is to be picked and how many are to be picked.
each of these methods requires a different type of equipment, which is more or less expensive.
Item-to-man picking: automation at the heart of the warehouse
New technologies are constantly revolutionising the operation of logistics warehouses. Automated picking was born out of these technologies: computerised processes guide the operators, such as voice-activated order preparation systems. Then automated mechanisms assist in the preparation of the parcels. This “item-to-man” picking can take place in two different ways
- Either robots bring the products to the preparation area;
- Or a central conveyor brings the products to be packaged to the preparation areas, as on industrial lines.
4. how do large warehouses manage their picking?
This is an interesting question, which allows you to look ahead to the issue of optimising picking, or even your entire supply chain. To do this, large e-commerce warehouses generally set up a storage system optimised for picking. This requires, in particular, the implementation of
- Dynamic shelving, racks and racks adapted to the chosen picking method;
- A precise labelling system, helping the order picker to optimise product traceability;
- Electronic terminals that allow the picker to locate the picking location and the place where to put the items for the packing phase;
- Handling equipment, such as order pickers, forklift trucks or pallet trucks, for example
other large warehouses, such as Amazon Prime, operate solely with a computerised system. In this case, it is only the data that determines the picking path of the operators. Remember: we spoke to you about this at the end of this article.
5. How can you adapt your picking method when you are starting out in e-commerce?
When you are starting out in e-commerce logistics, with a dozen or so orders per day and a small team, the organisation of picking does not require any particular strategy
- Picking can be done one order at a time, and each team member can perform different roles (picking, storage and packing).
- However, it is still essential to think about improving the management of your warehouse. The whole point is to optimise your flows, as well as the time spent on order preparation, to gain in efficiency.
this will involve the organisation of your storage methodaccording to
- The location of the articles and their recurrence of purchasein this case, a basic adaptation of the ABC storage method can be justified, but if you ship perishable products, you are obliged to adopt a FIFO method, whatever your shipping volume.
- The weight of your products: the heaviest products, which will be picked first by your operators, will be placed at the bottom of the shelves, while the lightest ones will be stored at the top.
in short, the more you have optimised your picking and warehousing, the more, when your warehouse becomes more professional, you will be ready to receive a large number of items and orders.
And, in this sense, the next step in your search for optimisation will then be to properly design your preparation table, from which all your shipments will start